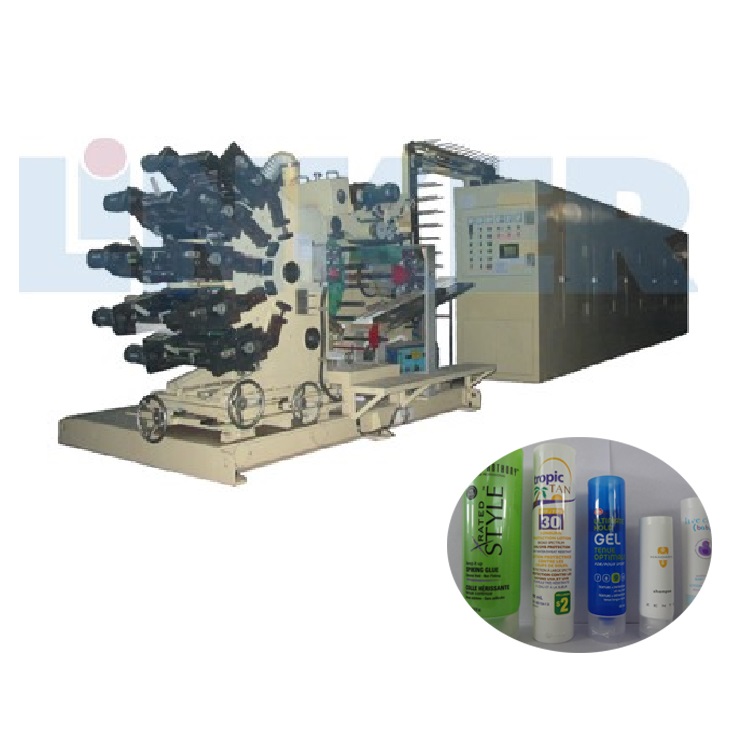
What is offset printing? Offset printing is a kind of lithography, it is very simple to say that offset printing is the use of rubber (rubber blanket) to transfer the graphic on the plate to the substrate printing method.It is also the existence of rubber blanket, this printing method is named. Rubber blanket plays an irreplaceable role in printing, such as: it can make up for the uneven surface of the substrate, so that the ink is fully transferred, it can reduce the water on the plate (see the role of water in printing) to the substrate transfer and so on. The above is only a general concept, we usually say offset printing may be more narrow, that is, there are three cylinders (plate, rubber blanket, impression) lithography printing, in the south of China, this printing method is called offset printing.
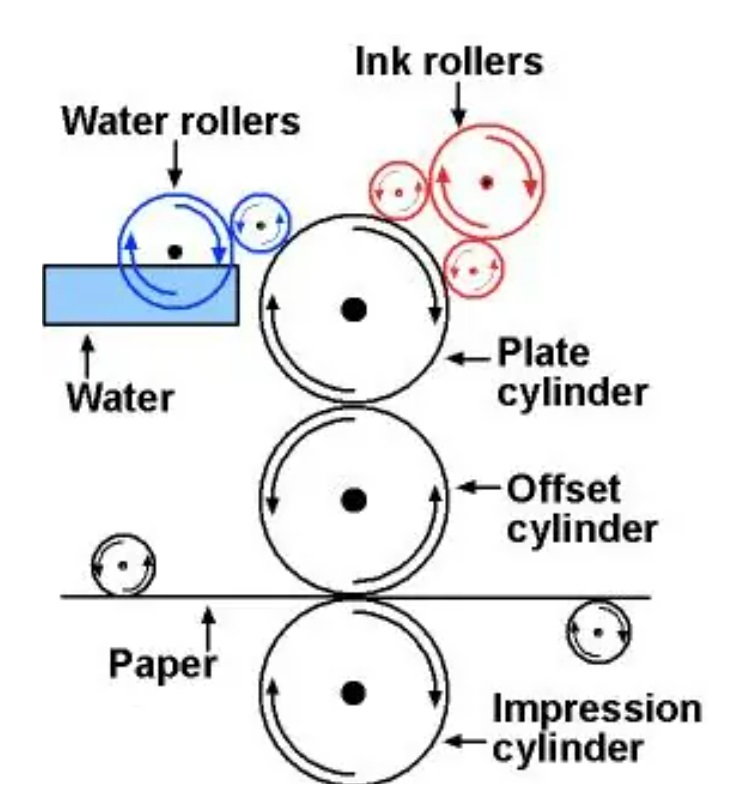
Introduction:
In China, offset printing is an absolutely dominant printing method, due to the advantages of fast printing speed, relatively stable printing quality, and short printing cycle, books, newspapers, and a considerable part of commercial printing are using offset printing. When it comes to printing, people immediately think of offset printing, Heidelberg, Roland, Mitsubishi, Komori and other foreign brands are also familiar to ordinary people.
Definition: Offset printing is the main way for Chinese label printing plants to print paper self-adhesive
Peculiarity: Fine graphics, rich layers, suitable for mass printing, and printing equipment can be used in one machine, suitable for the characteristics of the Chinese label market. However, sheet offset printing is not suitable for printing films with non-absorbent surfaces, because film labels are mostly roll-to-roll printing and require volatile drying inks.
Principles:
Water and oil are incompatible
The so-called similarity compatibility principle in chemistry determines that the slightly polar water substructure is different from the non-polar oil intermolecular polarity, resulting in the inability to attract and dissolve between water and oil, and the existence of this rule makes it possible to use water in flat printing to distinguish between graphics and blank parts.
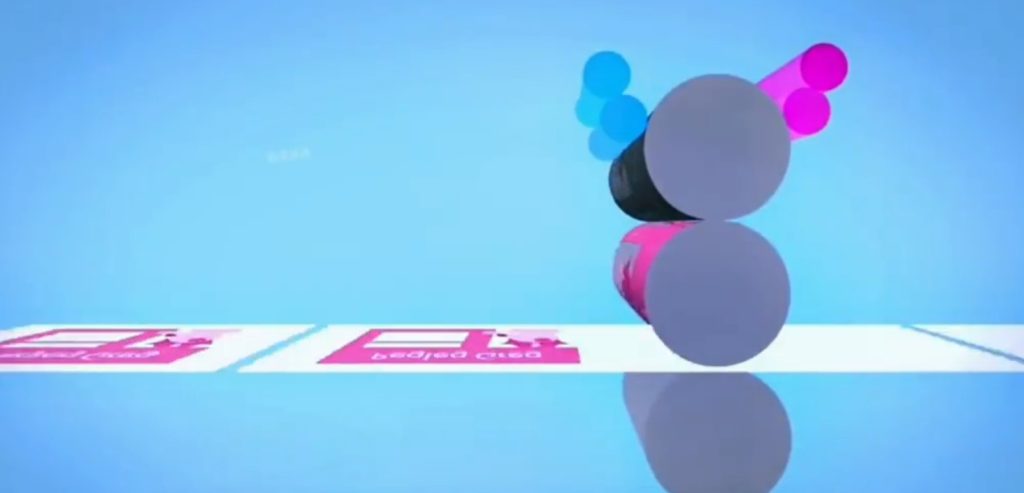
Selective surface adsorption
According to the different surface tension, it can adsorb different substances, which also provides the possibility for the lithographic offset separation.
Mesh image
Since the offset plate is flat, it is impossible to rely on the thickness of the ink to show the level of the text on the print, but by dividing the different levels into very small dot units that are imperceptible to the naked eye, it can effectively show a rich image level. In life, we have such common sense: the surface soaked by water is not easy to be contaminated by oil, and water and oil are always mutually exclusive. Since the offset plate is almost on the same plane, it is necessary to find a way to effectively distinguish between the blank part and the graphic part, and the role of water in the offset printing, we call it the principle of “water and oil insoluble”. In the printing process, first in the printing
The surface of the plate is evenly coated with a thin layer of water (in fact, due to the selective adsorption of the plate surface, the graphic part is not stained with water), and then the blank part is effectively protected when the ink is coated on the plate.
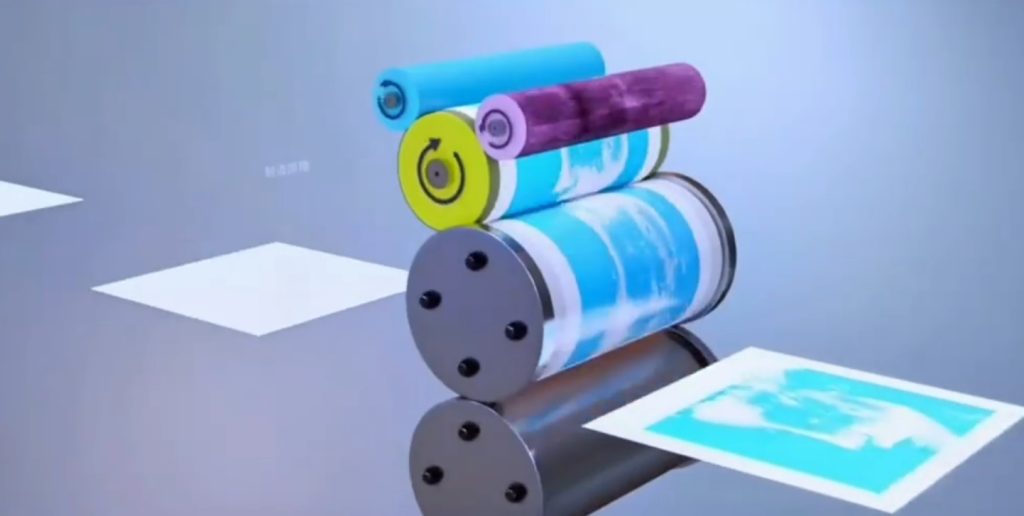
An effective solution to excessive emulsification of ink in offset printing
In the production of offset printing, we often encounter the phenomenon of excessive emulsification of ink, which not only seriously affects the production speed and product quality, but also causes certain economic losses. Excessive emulsification of ink is usually caused by too much water supply, so the operator generally takes the method of reducing the water supply and increasing the ink supply to solve it, but the adjustment effect can only be verified by printing, which undoubtedly wastes a certain amount of time and materials. To this end, we will ink excessive emulsification as a topic of research, through the search of printing press information at home and abroad, found that in dealing with such problems can learn from the Heidelberg CP2000 offset printing press used. Relative to each ink zone, an axial flow fan is installed in the moistening system, which can make the excess water in the area volatilize quickly. Inspired by this practice, we designed an adjustable drying system mounted on the offset press to allow excess moisture to evaporate quickly and reduce the chance of excessive emulsification of the ink.
It can adjust the distance between the axial flow fan and the plate cylinder through the DC low-speed motor according to the amount of water in the ink area, so that the excess water can quickly volatilize, and effectively solve the problem of excessive emulsification of the ink caused by too much water. The mechanism has the advantages of low cost, simple structure, convenient use, can be disassembled from the offset press at any time, does not affect the normal work of the offset press, and will not destroy the original mechanism of the offset press.
At the same time, in the test, we also found that due to the effect of blowing, the mechanism is also able to remove the paper wool caused by poor paper quality, thereby further improving the quality of the printed product.
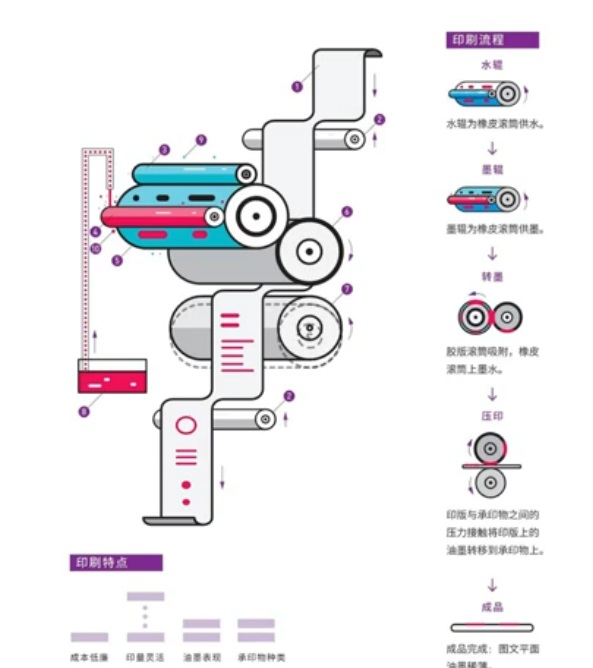
Technical knowledge
Register System
The degree of overprint accuracy. This is a common term for printing, and it is one of the important signs used to measure the printing quality of offset presses. The term registration applies only to two-color and multi-color printing. Its meaning is that when printing color printing pieces, the printing plate of various colors of graphics, accurately overlapping on the same print. And make the various colors of the dot is not deformed, the text is not out of shape, and the color is gorgeous, full of three-dimensional sense.
Without accurate overprinting, there is no printing quality. The requirement for accurate overprinting of color prints is the minimum and most basic condition. However, there has never been an absolute registration. According to the size of the paper, the number of network cables and the quality requirements of the printed products, the accuracy of the paper overprinting when printing color network prints should meet such requirements: the error of the paper on the printing position should be less than half of the distance between two adjacent dots. Generally speaking, it is within the range of 0.05 ~ 0.10mm. For some overprint quality requirements are not too high prints, can be relaxed to 0.15 ~ 0.25mm.
In order to facilitate the check of registration when printing, you can take the gage registration as a reference, and then carefully observe the picture and text overprinting, in order to see whether it is registered, often with 3 to 6 times the magnifying glass for observation.
Ink and wash balance
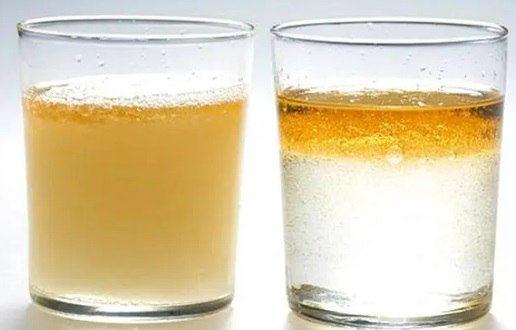
Ink balance is one of the basic principles of offset printing, which is based on the immiscible mechanism of oil and water. In mismissibility of ink and water is the basic principle of lithography printing, but offset printing, ink and water must be in the same plate at the same time, and maintain balance, so that the printing plate graphic part of the ink to maintain sufficient inking, but also to ensure that the blank part of the plate is not dirty, the balance between water and ink is called ink balance. Mastering the balance of ink and wash is a prerequisite for ensuring the quality of offset printing products.
Common paper
There are many types of paper used in offset printing, and the nature of various papers is also different. Even if it is the same type of paper, due to the different manufacturing processes of each factory, the quality will vary. The paper commonly used in offset printing is described as follows.
species
Offset paper (commonly known as Daolin paper) it is a paper commonly used for multiple color printing offset presses. Offset printing is often used to print a variety of publicity brochures, book covers, maps and trademark advertisements.
② Coated paper (also known as printing coating paper) it is coated with a layer of white paint on the surface of the base paper and made of high-grade paper after super calender processing. In offset printing, it is often used to print picture books, pictorial newspapers, calendars, calendars, product samples and refined illustrations.
③ Because of its hard texture, and has a large thickness and weight, some packaging decoration and trademark printing plants often use it to print various packaging boxes and trademarks.
④ Newsprint (commonly known as white newspaper) because of its soft texture, thin thickness and light weight, it is rarely used in offset printing, and only uses it to print newspapers.
peculiarity
(1) Offset paper has single-sided offset paper and double-sided offset paper. The weight of commonly used paper is 70g/㎡, 80g/㎡, 90g/㎡, 100g/㎡ and 120g/㎡. This kind of paper has the characteristics of small elasticity, compact texture, no depowder, no hair, and the paper surface has the appropriate smoothness.
② Coated paper has single-sided coated paper and double-sided coated paper. The weight of commonly used paper is 80g/㎡, 100g/㎡, 120g/㎡, 150g/㎡ and 200g/㎡. This paper has the characteristics of high smoothness, no dedusting, no delamination, and no bubble holes in the coating.
The white board paper has special grade and ordinary, single-sided and double-sided points. The weight of commonly used paper is 200g/㎡, 220g/㎡, 250g/㎡, 280g/㎡, 350g/㎡ and 440g/㎡. In addition to its white smooth, uniform thickness, compact texture and non-removal of powder wool, it also has the toughness of folding and not easy to break.
Newsprint can be divided into two kinds: web paper and flat paper. Its weight is generally about 51g/㎡. It is characterized by: soft paper, strong ink absorption, smooth paper and no fuzz. However, due to the soft paper, strong ink absorption and low water resistance, it is necessary to strictly control the moisture of the layout during printing to prevent overprinting and drawing.
⑤ Writing paper
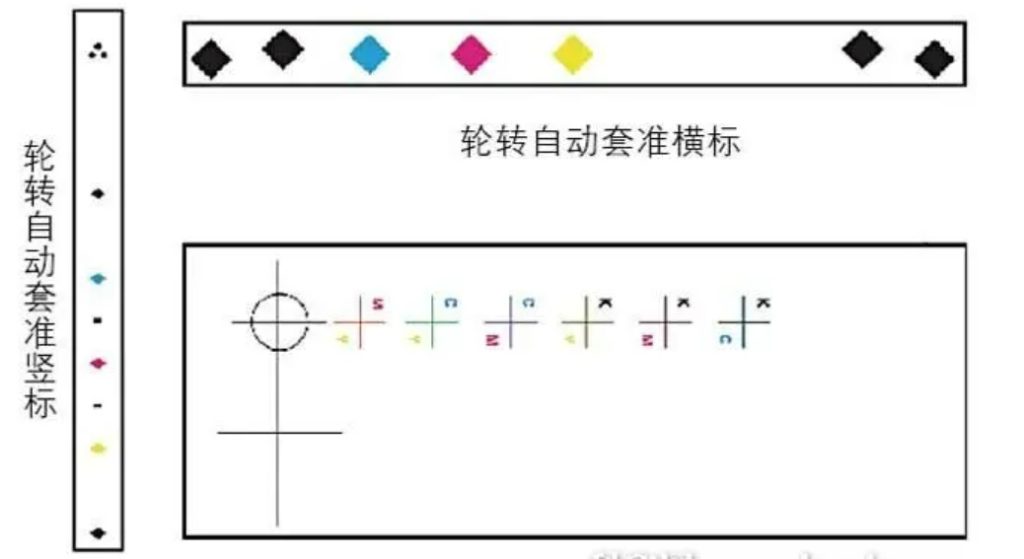
Printability
Printability refers to: paper, ink, printing process (stamping and printing speed), printing plate, ink roller and blanket, temperature and humidity of the printing workshop, etc., more suitable for printing conditions, in order to obtain high-quality printing products.
Ink viscosity refers to the degree of viscosity during flow, which is an indicator of ink fluid flow resistance. The viscosity of offset printing ink mainly depends on the inherent properties of the binder used and the size and content of the pigment particles and their dispersion state in the binder. High pigment content, large ink viscosity; The pigment particle is large, the ink viscosity is small; The pigment dispersion is good, the ink viscosity is small. In the offset printing process, a certain viscosity is the main condition to ensure the normal transfer of ink, and it is also an important condition to determine the fastness, clarity and gloss of the ink printing. When the ink viscosity is too large, the transfer and transfer of ink are difficult, which is easy to cause insufficient ink in the layout, resulting in flower plate; If the viscosity is too small, it is easy to produce floating dirty, which will cause excessive emulsification of the ink or make it unable to maintain normal transfer and transfer, and gradually accumulate on the ink roller, printing plate and rubber sheet. When accumulated to a certain extent, it will cause paste.
Ink permeability refers to the permeability of the ink layer transferred on the surface of the printing sheet, which is to characterize the permeability phenomenon and properties of the ink in the early stage of the drying process. In the offset printing process, the ink penetration process includes two processes, that is, the instant rapid penetration process that occurs at the moment of printing pressure action and the slow free penetration process after the printing pressure is small.
In the offset printing process, the permeability of the printing ink mainly depends on the nature of the binder itself, but also related to the printing pressure, printing speed and the type of paper used, surface properties, etc. The penetration of the general ink layer on the paper shows different permeability properties and penetration speeds due to different ink types and different viscosity, and the permeability of the oxidized conjunctival ink is usually smaller than that of the permeable gel conjunctival ink. The permeability of ink plays an important role in the solid drying of imprinted ink layer and the color reproduction, gloss and friction resistance of ink layer after conjunctiva. When the permeability of the ink and the ink absorption of the paper are too strong, it is easy to cause powder, through printing and other phenomena, so that the color, gloss and friction resistance of the imprinted ink film are significantly reduced. When the permeability of the ink is too small, it will cause the back of the sheet to stick dirty, serious will make the stack of sheets stick to each other.
Color mix
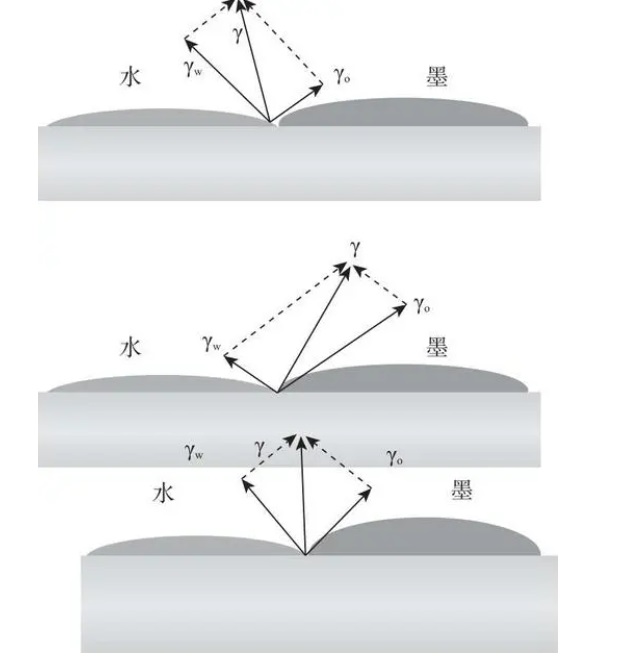
In the process of offset printing, the phenomenon of red, yellow or blue that is inconsistent with the color of the printed product and the proofing proof often occurs, or the color mixing failure after the pattern picture is overprinted, which will affect the product quality, and will cause the whole batch of products to be scrapped and make the enterprise suffer serious economic losses. In this paper, combined with their own experience of many years engaged in offset printing process work, summed up their own views, in order to discuss with peers.
Printing color bias and color mixing fault can be roughly summarized into four aspects of the reasons: (1) plate making operation is not standardized caused by yellow, magenta, green a color printing plate dot is too deep or too light;
(2) improper deployment of ink color or three primary color inks do not match;
(3) the printing color sequence arrangement is unreasonable;
(4) The printing paper itself has a more serious color bias phenomenon.
Color deviation caused by plate dot depth fault
In the process of printing plate, the intensity and spectrum of the printing plate light source do not match the photographic characteristics of the printing plate adhesive, or the exposure time is improper; The pH value of the developer and the length of the development time are not appropriate, which may cause the printing plate dot to be too deep or too shallow. Such a plate on the machine printing, the picture color bias is inevitable.
Therefore, the quality of the plate must be identified before the plate is on the machine, the identification of the plate dot can be compared with the yellow, magenta, blue, black original film with a magnifying glass, carefully look at the corresponding plate pattern of the same part of the bright tone, medium tone, dark area dot appearance, that is, the bright part of 2% of the small dot, the plate should be equally exposed. 3% of the print outlets should be able to print. If 2% of the small dots on the printing plate are not exposed, it means that the printing plate is shallow and not applicable. Using the method of identifying 2% of the small dots on the same part of the film as the printing plate, identifying 97% of the dark dots on the same part of the original film. If this bit of dot on the plate and paste, it means that this plate is sun-deep; If the area of the blank area between the dots is expanded, it means that the printing plate is shallow and should be re-dried. Of course, in the case of conditions, the use of Brunel signal bar to control the quality of printing, it can be accurate and easy to operate. The identification method is to observe 12 Yin and Yang dots in the fifth 50% fine mesh test block of Brunel signal bar on the printing plate with the help of a high-power v magnifying glass. The area of Yin and Yang dots should be 6 in order from large to small. 2% of the small dots in the 6 small cells of the sixth block should be exposed, if 3% of the printed plate’s dots exist, and 2% of the dots disappear, it means that the plate is light. On the contrary, not only 2% of the dots exist, but also 1% of the small dots exist, indicating that the printing plate is too deep.
Color deviation caused by ink problems
In the printing process, the color deviation fault caused by the ink is mostly because of the different degrees of color deviation of the three primary colors produced around the existing ink, such as Peony brand 05-24 yellow (red 0.16), 05~32 sky blue (red 0.35), which will affect the color deviation of the whole picture to different degrees, especially the middle tone. However, a small amount of color bias can be corrected from the ink compatibility. For example, a group of three primary colors used in East China for a long time, Like 05-28 transparent yellow, 05-14 magenta, 05-32 sky blue produced by Shanghai Ink Factory and GS-135 magenta, GS-425 sky blue, GS-236 medium yellow ink produced by Tianjin Ink Factory have the characteristics of fast drying, fast fixation, bright color, less color, strong hydrophobicity, good printability, etc. It has played a good role in high speed and multi-color machine for fine products printing on coated paper.
Color deviation caused by color sequence arrangement
Compared with the proof, sometimes although the ink, paper and field density used are the same, the print still has yellow, red or blue or overprint color ink mixing phenomenon. What is the reason for this? First, the proof press is generally monochrome wet press dry printing, ink adsorption, transfer rate is more appropriate; Second, the machine structure, pressure and speed are not the same as the actual printing; Third, the color sequence arrangement of high-speed multi-color printing is unreasonable. The unreasonable color sequence arrangement will not only cause the color deviation fault, but also make the printing pattern color due to wet press wet overprinting resulting in color mixing consequences.
Multi-color machine printing color sequence arrangement should follow the principle
- First deep, then shallow
According to the order of 4-color printing ink brightness difference, that is, dark color printing first, light color printing after. - Start small and then big
According to the printing plate graphic area arrangement. That is, the printing plate with small graphic area is printed first, and the graphic area is large. - Ink with high viscosity is printed first, and ink with low viscosity is printed later
According to the order of ink viscosity, the ink with large viscosity is printed first, and the ink with small viscosity is printed after. Such as Shanghai Peony brand 05 black ink 1188.2Pa, blue ink 488.5Pa > magenta ink 477.1Pa > yellow ink 147Pa order arrangement. For the ink with large viscosity that must be printed in the back color group, its viscosity should be properly reduced first, which is crucial, otherwise it will cause the reverse overprinting of color mixing defects. - The color ink with large coverage force is printed first, and the color ink with small coverage force is printed later
According to the transparency and coverage of the ink arrangement, that is, the ink with low transparency and large coverage force is first followed by the ink with high transparency and small coverage force, which can improve the color effect after the ink is overprinted. - Weak color print first, strong color print after
The color sequence is arranged with the characteristics of the original manuscript, the monochrome machine belongs to the wet press and dry embossed method, mostly using the color sequence of yellow, magenta, green and black, or the color sequence of yellow, green, magenta and black, which is based on the overprinting between the colors of the multicolor sheet paper, at least a few hours apart to overprint the next color, which may cause the paper to expand. From the perspective of visual overprinting requirements, the first color first prints weak yellow ink, even if the printing sheet is telescopic, the limited error impact of the later color sequence blue, magenta, and black overprinting is not obvious. Two-color printing machine adopts alternating color sequence of light and dark ink, that is, yellow, magenta and green, black sequence, or yellow, green and magenta, black color sequence.
In short, as long as the offset operator can carefully and dialectically understand the main regular causes of color bias and color mixing failures, and take corresponding preventive measures in a targeted manner, it can be prevented before it occurs and receive twice the effect with half the work.
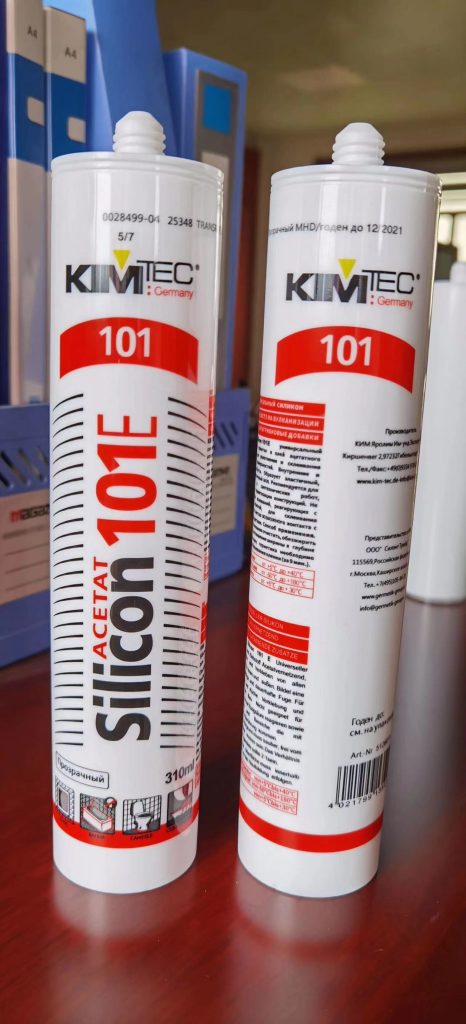
press run
Improving plate printing resistance is a key link to reduce raw material consumption, reduce product production costs, shorten production cycle and improve economic benefits. In practical work, the following methods can improve the printability of the printing plate.
1, strictly printing raw materials into the warehouse. In particular, we must ensure the purchase of high-quality paper and high-quality PS plates. Like 52g/m2 for printing books? 60g/m2 book and magazine paper, if the procurement staff is eager to buy cheap inferior paper from informal paper manufacturers, the whiteness, uniformity, smoothness, finish, surface tension, sizing and other technical indicators of the paper can not meet the printing requirements, the paper surface is rough, the paper ash is large, and the fine sand is more, which is easy to wear the photosensitive resin film of the PS plate. Reduce the printability of the plate. Therefore, in order to improve the printing resistance of offset printing plates, we must first start from the purchase channels of materials. Unqualified raw and auxiliary materials shall not enter the factory or the warehouse. At present, there are many brands in the printing materials market, it is difficult to distinguish between good and bad, printing companies should shop around when buying materials, ensure quality, and buy high-quality printing materials.
2, to master the correct PS version exposure time. Pay special attention to the amount of exposure, do not overexposure, so as not to affect the printability of the printing plate. Under normal circumstances, the four-color separation film requires 3% of the small dot is not lost, 98% of the large dot is not paste; Patterns, lines, text clear, small graphics do not fall out of the version, the writing pen full and bright, no lack of pen breaks.
3, PS version developer concentration should be strictly controlled. When preparing the developer, it is necessary to prepare the developer in strict accordance with the instructions of the manufacturer. The developer or developer powder, sodium hydroxide, and water are measured accurately by the measuring instrument. Do not prepare or dilute the developer by feeling based on experience. If excessive exposure during the printing process, the concentration of the PS version developer solution is too high or the water temperature is too high, it will directly reduce the printability of the PS version.
4, by baking PS plate to improve the printing rate of the plate. Many printing manufacturers on the long plate live, print more books, newspapers and other products printing using the method of baking plate to improve printing resistance, that is, PS plate after the printing of dirty, wipe baking plate liquid, with a folios electric oven for baking. ① Before baking, be sure to pay attention to clean up the dirt and dirty points on the blank part of the PS plate with retouching paste, otherwise it is difficult to remove the dirty points after baking. ② The towel used to wipe the baking liquid is not clean, or the fibers on the towel fall off on the PS plate is also easy to be dirty. ③ The baking plate temperature is 200 ~ 220℃, the baking plate time is generally about 10 ~ 15 minutes, should not be too long, but also according to the temperature resistance of the photosensitive resin film of the PS plate to specify the baking plate time. If the photosensitive film baked out of PS plate is light brown color, brown red, like the color of ripe plums, indicating that the baking plate is appropriate; If the baking time is too long, the temperature is too high, it will roast the photosensitive resin film of the PS plate, or make the plate base soft.
- Before printing, check whether the density of the film is suitable, the text, lines, and pattern blackness on the sulfate paper should be full, no lack of pen breaks, large characters and wider lines should not be output again, and can also be baked on the electric stove, which can play a blackening role. When baking, it is necessary to prevent the sulphate paper from wrinkling, which affects the drying plate. Printing batch of large books, trademarks, packaging and decoration products, whether it is a film, or a sulphate paper, the strokes and lines of the text as thick as possible, accordingly, it will be more resistant to printing. Density and blackness can not meet the requirements, can not be accommodated, rework and redo, in order to ensure the printing resistance of the PS version.
6, the pressure of the water roller on the plate should not be too large. When debugging the two water rollers and the plate pressure, it is best not to use the good plate of formal printing, and the used PS plate can be used to debug, so as not to damage the plate. At the same time, the thickness of the liner paper in the plate drum should be appropriate. The pressure of the water roller on the printing plate is too large, the graphic wear of the printing plate will increase, and the printing resistance will be reduced. - When loading the plate, check whether there is wrinkling, discounting, paper scraps and small paper blocks on the back of the plate. If there are these conditions, remove the lower plate and arrange the liner paper.
- When printing the plate and repairing the plate after loading the machine, the residual retouching paste was accidentally applied to the photosensitive resin film of the PS layout text, which played a role in thinning the film and also affected the print-resistance of the PS plate. In addition, after the edition of the page with dirty, often use cloth with wetting powder to wipe the version to dirty. However, do not use too much force when wiping the plate with wetting powder, and do not wipe the time for too long, otherwise the photosensitive resin film of the printing plate is not resistant to printing after being wiped thin.
- Use less pressure when printing. After the plate is installed on the plate drum, the pressure between the plate drum and the rubber drum should not be too large, the thickness of the PS plate and the lining paper should not exceed 0.65mm, and the thickness of the rubber sheet and the lining should not exceed 3.25 ~ 3.40mm (measured with a micrometer). The plate should be pressed and compacted to prevent relative slippage during the operation of the offset press. In addition, accurately adjust and control the pressure between the inking roller, the water roller and the plate cylinder of the offset press to avoid direct wear of the layout.
10, strict control of ink balance in the printing process. Pay attention to control the thickness of the ink layer to avoid spreading the ink to the blank part of the plate. If the ink is too thick, the tiny particles of the color material, bonding material and adhesive material in the ink will increase the friction effect on the printing plate, and will also accelerate the wear of the printing plate. Maintain normal water supply, under the premise of non-stick ink in the blank part of the printing plate, use the minimum water consumption to moisten the layout, in order to reduce paper deformation, ink emulsification, inaccurate overprinting, ink dilution and other phenomena. If the layout is too much water, combined with weakly acidic water tank liquid (used to clean oil), it also has a corrosive effect on the printing plate. Maintain the balance of ink and wash, but also avoid the phenomenon of dirty version, flower version and drop version caused by improper ink and wash.
11, prevent plate surface oxidation. In the offset press halfway down or lunch and rest, be sure to wipe gum Arabic, so as to avoid long-term exposure to the air of the plate, resulting in plate oxidation and reduce the printability of the plate.
12, prevent debris and layout wear. Also be careful not to let the paper transport process double, multiple and other debris to the plate crushed.
Offset feature
Offset printing adopts automatic assembly line operation, computer automatic control, printing tower roller rolling printing, transmission belt automatic transmission CD. In order to avoid mixing different types of discs, add BASLER R2 to the input side for automatic detection. Offset printing is mainly a white background and the different proportions of the four main basic colors (black, blue, red, yellow) to adjust a variety of printing colors. The depth of various colors is determined by the length of printing time, printing pressure, and printing temperature. The longer the printing time, the darker the color; The greater the printing pressure, the darker the color; The higher the printing temperature, the darker the color.
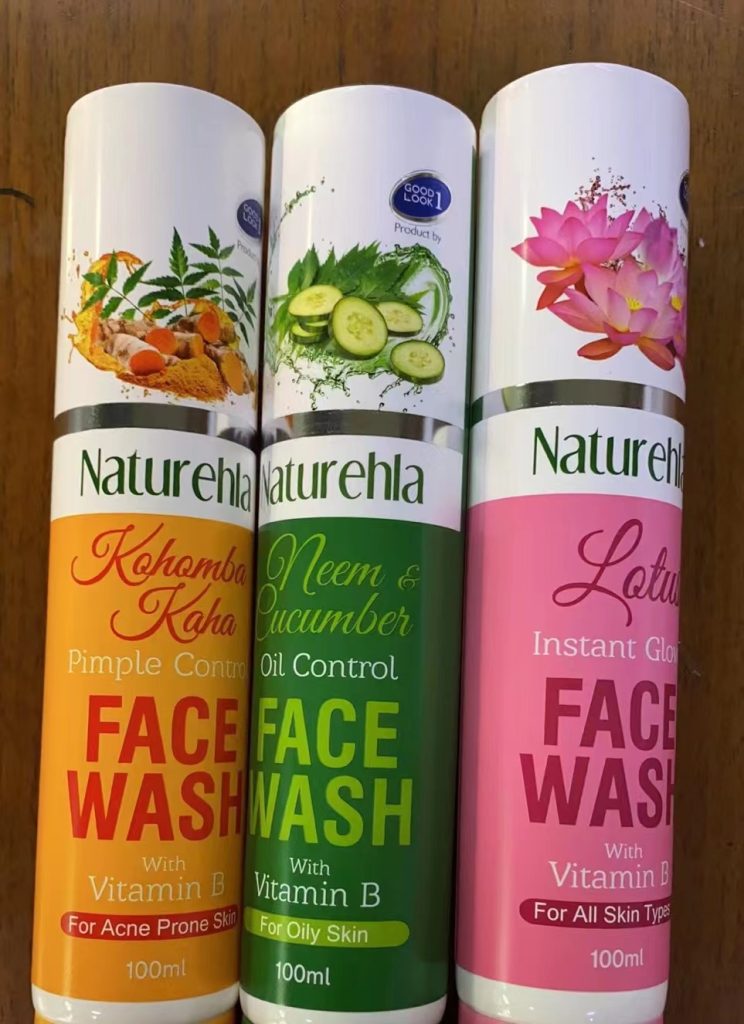
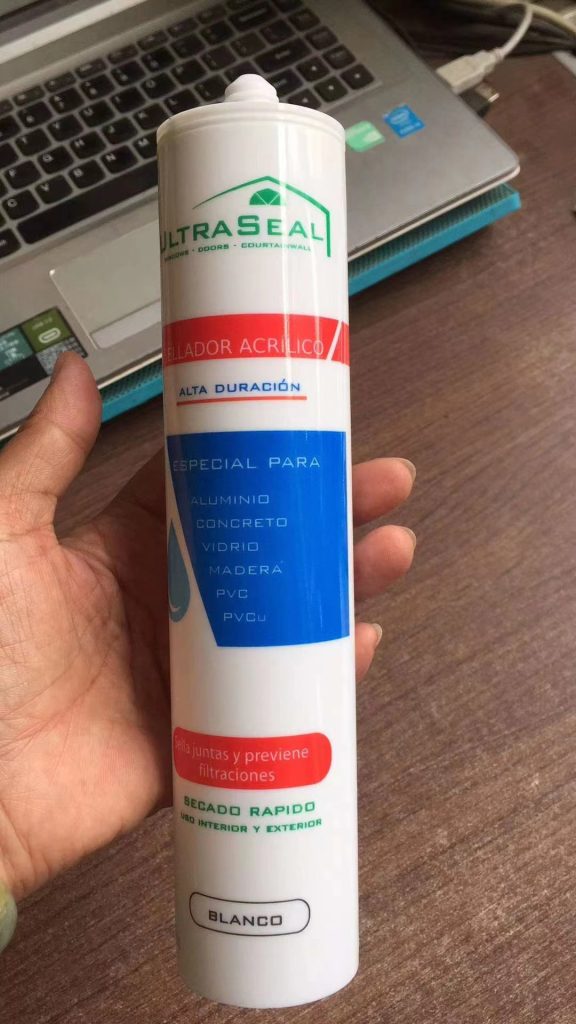
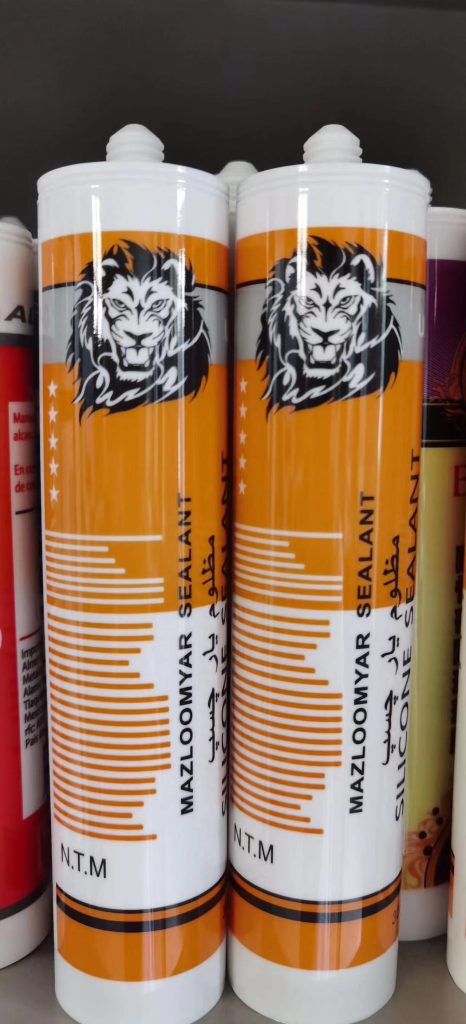
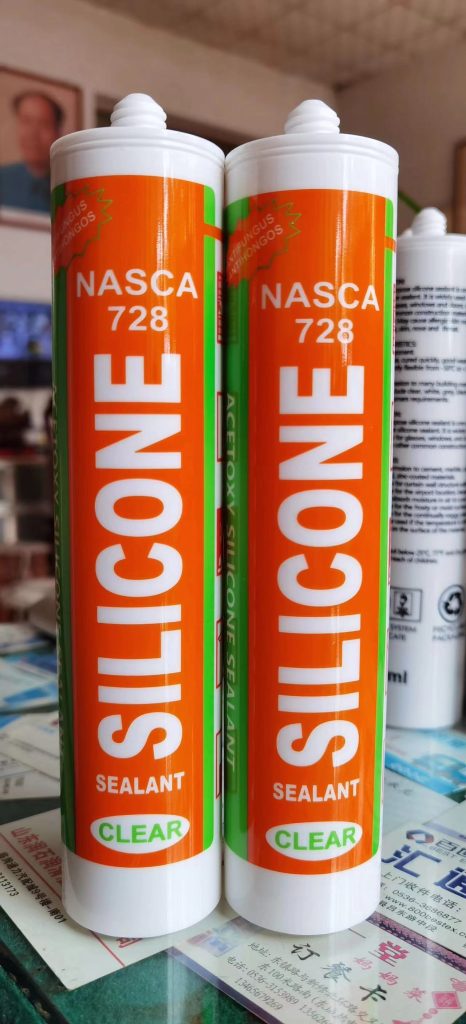
- Offset printing has the characteristics of high efficiency, high quality and low cost compared with screen printing.
- High efficiency. Offset printing adopts automatic flow operation, machine automatic color, computer automatic monitoring, fast speed, can print 15,000 pieces per hour.
- High quality. Computer fine tuning, accurate color, high position accuracy.
- Good color effect. Printing glossy oil, glossy color, smooth surface, clear printing effect, not easy to fade.
- Low cost. Offset printing using roller printing, thin printing layer, less oil.
Other Type of Printing
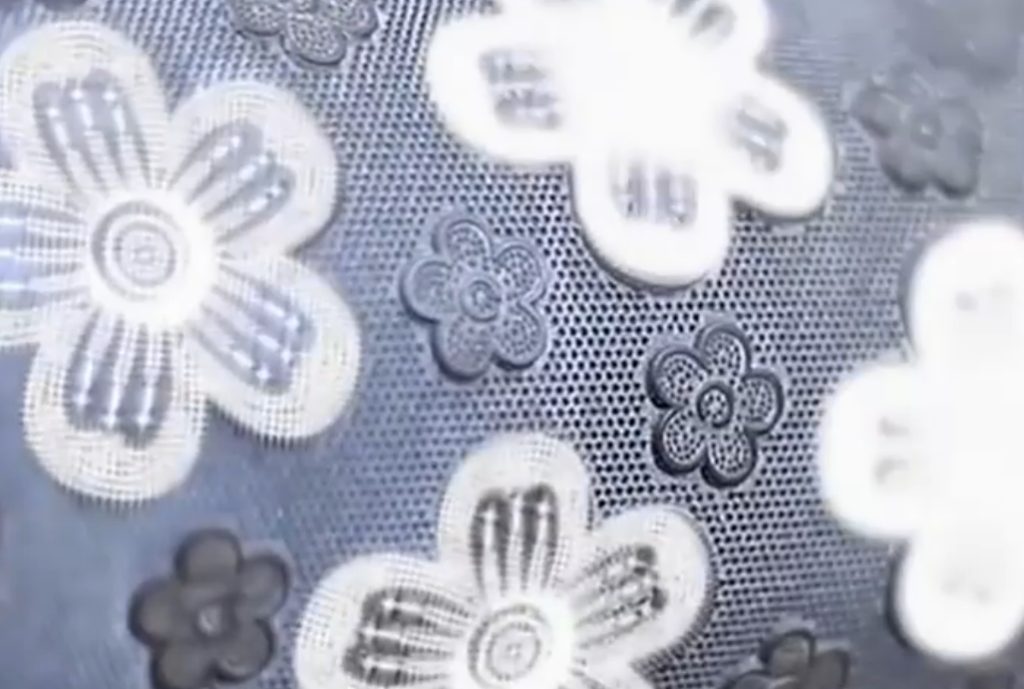
First, letterpress printing
More text, fewer photos and drawings, more opportunities for change of text, small print quantity – hundreds or thousands of prints are suitable for letterpress printing. The number of print times should not exceed 30,000, and the fine picture electroversion should not exceed 70,000 or 80,000. Print pictures must use powder paper to get the perfect dot. So you can’t use cheap paper to print pictures and hope to get beautiful results. When the table is lined with letterpress, the intersection of the lines is easy to separate and disjointed, which is a common shortcoming. In addition, the printing pressure is too high or the pressure cylinder surface is too soft, which will cause the back of the finished sheet to have an embossed bulge, which will greatly reduce the quality of the printed matter.
Two, gravure printing
Intaglio printing is suitable for printing high quality and expensive publications, whether four-colour or black and white images, intaglio printing can be highly attractive to photography. Due to the high cost of plate making, the printing volume must be large, so in Hong Kong is the least used of the five types of printing.
Three, screen printing
Because the screen printing ink is particularly thick, it is best used for special effects, and the number is not large and the ink color needs to be thick. It can also be printed on the stereo such as square boxes, boxes, round bottles, cans, etc. In addition to paper, the printing base can also be printed with cloth, fast handle, plywood, plastic sheet, metal sheet, glass, etc., which is commonly used for printing pennants, T-shirts, tile boxes, soda bottles, circuit boards, etc. The above various printing characteristics are not possible with other printing methods.
Four, plastic plate printing
Plastic plate printing is only suitable for printing plastic bags, hand drawn, large and small plastic packaging. The input printing machine is not a single sheet but a roll, and after printing, it should be cut sheet by sheet. The fineness of printing points and lines is far less than that of letterpress and offset printing, so it can be seen that offset paper printing cannot be used to print books and publications.
Five, network printing
With the rapid development of the Internet industry, as well as the market’s familiarity with and recognition of e-commerce, network printing is also more and more recognized by the market. The annual printing business volume of Taobao alone is as high as 2.8 billion yuan, and the total output value of e-commerce printing exceeds 40 billion yuan. Among them, business short printing is the main. With the development of computer technology and the popularity of network e-commerce, network printing is increasing at an annual rate of more than 200%, and it is expected that the proportion of national network printing will reach 8% by the end of 2012. European and American e-commerce printing started earlier, accounting for 78% of the entire printing industry, and began to develop in the direction of personalization, digitalization, and three-dimensional.
In 2011, the global printing industry output value reached 720 billion US dollars, of which North America accounted for 28%, Europe accounted for 31%, Asia accounted for 30%, and other regions accounted for 11%. Among them, the printing industry in Asia has developed rapidly, especially in China, which has maintained a double-digit growth rate in recent years. According to the statistics of the National Bureau of Statistics by the end of March 2012, there were 106,800 printing enterprises in the country, with 3,875,600 employees, and the total industrial output value exceeded 1 trillion.
Network printing solutions
(A) Business integrated printing network platform
Comprehensive printing solutions and DIY personalized ordering system; Print network operations, efficient business management and production management. Suitable for: large commercial printing enterprises, it can be used as a comprehensive portal website for enterprises, or it can create different brands to operate separately.
(2) “Network Printing Platform”
Provide enterprise characteristics of the network printing website, including printing network ordering system, a variety of printing quotation system and integrated production process management. Printing enterprises, fast printing enterprises, commercial short printing enterprises, suitable for the implementation of network printing applications of small and medium enterprises. Such as the domestic well-known iein printing kung Fu network printing platform.
(3) “Personalized customization platform”.
Provide online and offline personalized product making tools, so that customers WYSIWYG completely personalized experience; A wide range of products, providing personalized products including all kinds of gift books, personality albums, mugs, T-shirts, throw pillows, mouse pads and a variety of sculpting jewelry; At the same time, it provides a variety of e-commerce styles and interfaces, close to customers’ favorite operations and processes, and attracts more customers to use and order products. Applicable industries: printing industry, imaging industry, fast printing industry, and personalized product customization needs of enterprises.
Reference:
- Zhang Hai-Yan, Zhang Wei. Research on computer simulation of offset printing ink delivery system design. CNKI;WanFang, 2003
- Wang Yiming, CAI Jifei, Zhao Jibin. Research status and progress of key technologies of high-speed offset press. CNKI; WanFang, 2007,
- Bai Ziyou, Liu Shiwei. Research on Dynamic simulation model of offset press ink roller. Packaging Engineering, 2004
- Zhao Qing-hai. Design and calculation of cylinder balance of high speed sheet-fed offset press. CNKI, 2002
- Wu Yue-Qing, Wang Min, Zheng Jun. Analysis of JDF work summons and development of communication interface for offset lithography. CNKI;WanFang, 2007
Offset Printing Machine Manufacturer
We have 1-8 color offset printing machine for soft tube and hard tube. Soft tube used for cosmetic tube, hard tube can use for glass cement. This machine is also suitable for bottle, cup, lip gloss bottle or any tube and bottle offset printing. Six color offset printing machine is the most popular product welcomed by customer. The difference of soft tube and hard tube printing machine is only the length of dry oven. The soft tube use long oven 8-9 meters, the hard tube use the short oven 2-4meters.