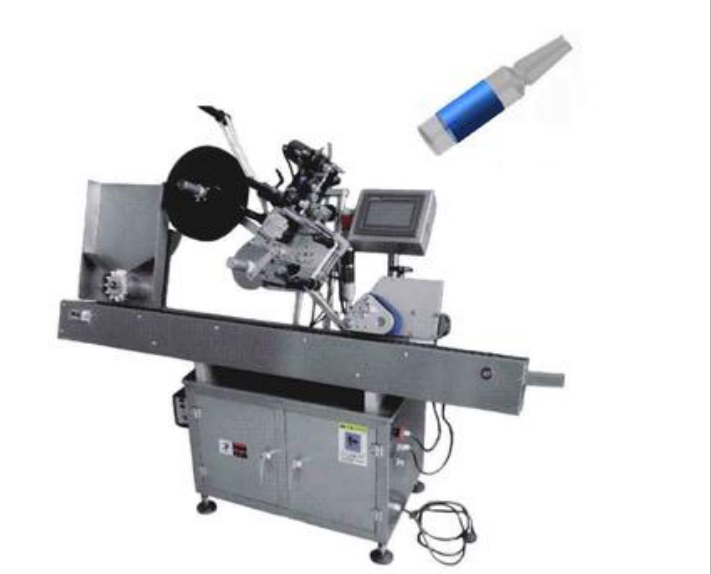
- Width of Label: 20-100mm;
- Length of Label: 20-150mm;
- Speed: 20-40pcs/minute;
- Bottle diameter: 18-20mm;
- Accuracy: within 1mm;
- Price: 500USD.
Product Information
Round product labeling machine:
Round product labeling machine including round jar, round bottle, round tube labeling Machines.
Round Jar Labeling Machine:
A bottle with a relatively large mouth. Wide-mouth glass bottles are often used in laboratories to hold solid drugs.
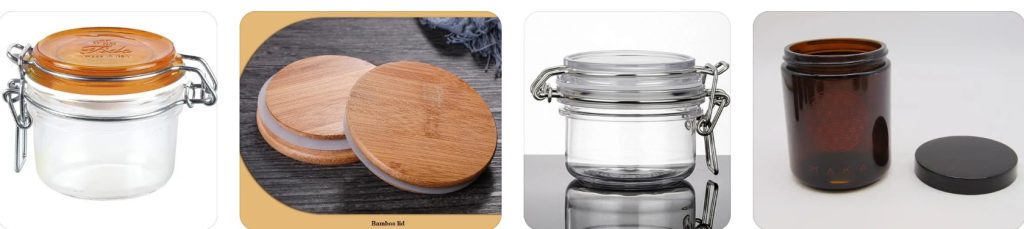
Round tube labeling machine:
Tube including the soft tube, hard tube, such as cosmetic soft tube, PE tube, PP tube, Plastic tube, ABL, PBL, Aluminum tube, glass cement hard tube, vitamin C Pp hard tube and so on.
Manual round labeling machine:
Manual round labeling machine is a semi automatic labeling machine which operated by workers. The machine is small and capacity is about 20-40pcs per minute.
Automatic round bottle labeling machine:
Automatic round bottle labeling machine is feeding and labeling and output automatically. It can also connect with filling and capping machine and other packing machine as a production line.
Round Bottle Labeling Machine
Round labeling machine is mainly used to attach labels or films on the circular surface or small conical surface of round bottle objects. These equipment are widely used in many industries, including but not limited to pharmaceutical, food, cosmetics, electronics, hardware, plastic and so on. specific application examples include sterilized water bottle labeling, gel water double labeling, red wine bottle calibration labeling, solid glue bottle labeling, oral liquid bottle labeling, pen stick labeling, lipstick labeling, etc. round bottle labeling machine is not limited to single label, can also be affixed double labels, right back double label spacing can be adjusted flexibly, is suitable for self-adhesive label, non-adhesive film, electronic supervision code, bar code and so on. Some high-end round bottle labeling machines are also equipped with a circumferential positioning detection device, can realize the designated position on the circumferential surface labeling, further improve the labeling accuracy and efficiency. In addition, part of the round bottle labeling machine can also be matched with ribbon coding machine and inkjet coding machine, to print the production date and lot number on the label, to realize the integration of labeling and coding, to meet the needs of different users
With the continuous progress of technology, the development of enterprises gradually turned to the continuous innovation of technology, the change of The Times, technology is the only sign, the continuous development of the commodity economy requires that the automatic labeling machine should be technically up to standard when facing the market.
Technological innovation, automatic labeling machine is only half of the success in the development of the market. With the continuous improvement of the degree of mechanization, packaging machinery in the domestic market has begun to transform in the direction of automation and intelligence. Mechanical automation is the standard for the development of modern manufacturing enterprises, is the beginning of the machinery to a higher development point, Through our continuous efforts, constantly learning and summarizing advanced technical experience at home and abroad, on the basis of the use of a unique mode of thinking to achieve the real situation of innovation, for the current automatic labeling machine has a reasonable design, easy to operate, Stable performance, low failure rate, long service life, but also has the advantages of humanized touch screen: simple and intuitive operation, complete functions, with a rich online help function, a wide range of use, all kinds of flexible packaging materials can use automatic labeling machine for automatic labeling.
With the continuous development of the market economy, the fierce competition determines that the development of enterprises must constantly adjust their own development strategy and marketing strategy, and constantly create the advantage of survival in the market. For some developing enterprises, having a certain market advantage is equal to having a market, and automation technology has achieved the development opportunity of automatic labeling machine. And its good work efficiency and labeling effect for enterprises to save labor and cost at the same time, so that it quickly into the market, and become one of the important equipment in the packaging industry, automatic labeling machine is generally suitable for pharmaceutical, food, daily chemical and other industries of round bottle labeling, can be affixed to the full circle labeling and semi-circular labeling, optional automatic turntable bottle management machine. It can be directly connected to the front-end production line, automatically feed bottles into the labeling machine, and can be configured with ribbon coding and labeling machines.
We are a professional labeling machine manufacturer focusing on independent research and development, design, production and sales. Long-term focus on the field of automatic labeling machine, continue to study automatic labeling machine technology, independent research and development of automatic labeling machine, round bottle labeling machine, flat labeling machine and customized labeling machine with automatic production line.
Abstract: Plane labeling machine, automatic labeling machine, automatic round bottle labeling machine, labeling machine manufacturers
What is Round Bottle Labeling Machine:
The round bottle labeling machine is a device for attaching paper or metal foil labels to specified packaging containers with an adhesive. Labeling machine is an indispensable part of modern packaging. The types of production labeling machines in China are gradually increasing, and the technical level has also been greatly improved, which has shifted from the backward situation of manual and semi-automatic labeling to the pattern of automatic high-speed labeling machines occupying the vast market.
Working Principle:
Core working principle: After the bottling mechanism separates the product, the sensor detects the product passing, returns the signal to the labeling control system, the control system controls the motor at the appropriate position to send the label and attach it to the product to be labeled, the product flows through the labeling device, the labeling belt drives the product to rotate, the label is rolled over, and the attaching action of a label is completed.
Operation process: Put the product (can be connected to the pipeline) – > Product delivery (equipment automatic realization) – > product separation – > Product detection – > Labeling – > Labeling – > Collection of labeled products.
Parameter
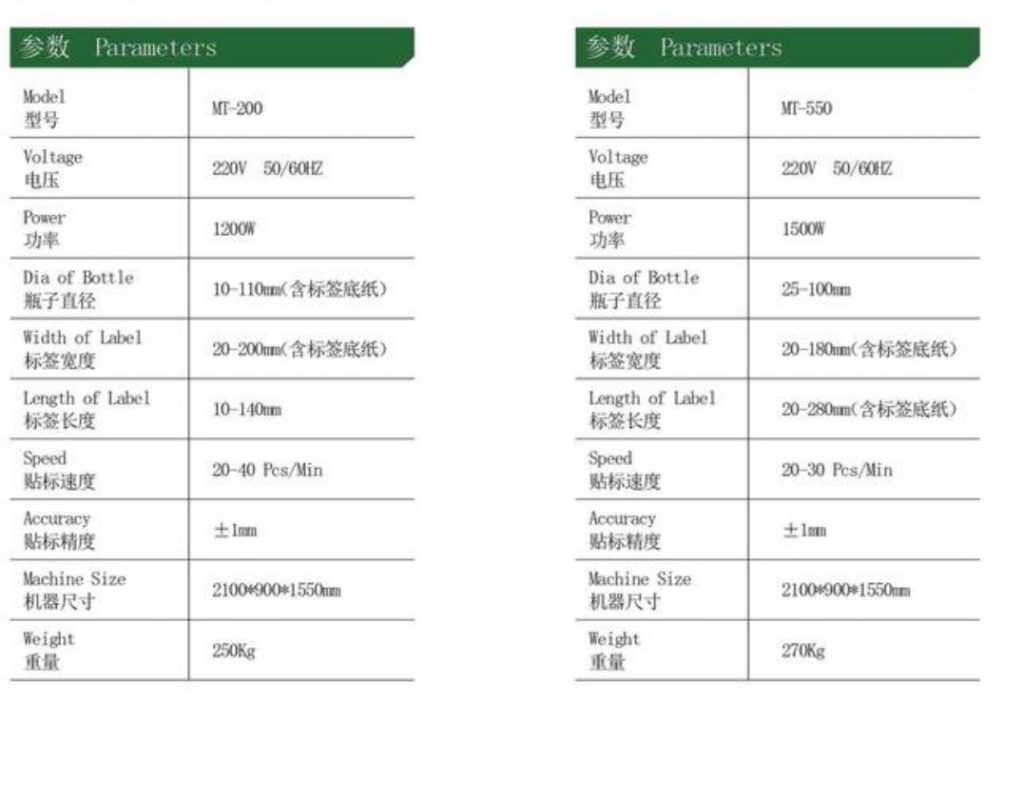
Feature:
The utility model relates to a vertical round bottle labeling machine, which comprises a cabinet, a conveyor belt, a mark feeder and a mark holding device. The conveyor belt is installed on a cabinet, and the mark feeder is fixed on one side of the conveyor belt. The beacon device mainly comprises a beacon conveying mechanism and a beacon plate. The beacon conveying mechanism comprises a driving wheel fixed on one side of the conveyor belt and a beacon conveying belt arranged on the driving wheel. The utility model has the advantages that the holding device adopts a conveyor belt type, corresponding to a holding plate with a rubber layer, which can increase the distance of pushing the bottle after labeling, so that the pasted label is posted more firmly, and the holding plate can adjust the holding with the size of the round bottle by adjusting the distance between the front and back of the holding plate The distance between the front and back can be adjusted with the size of the round bottle .
Automatic round bottle labeling machine intelligent labeling of cylindrical products of different sizes in food, medicine, daily chemical and other industries; Servo or German original imported labeling engine option to meet the needs of different customers; Feed and receive turntables can be selected for stand-alone operation to improve production efficiency;The contact position of the bottle board and the rubber layer reduce the damage to the label, making the labeling process smoother. The occurrence of label folding is reduced.
The bottle labeling machine uses self-adhesive roll labeling paper, and the labeling process is completed by rolling labeling. The self-adhesive labeling machine has clean and sanitary, no mold, beautiful and firm after labeling, and will not fall off by itself.
Standard operating procedure SOP for round bottle labeling machine
First, boot preparation
1) Confirm whether the label volume meets the specifications, install and check it as required; (If there is any change in product specifications, please refer to Annex 5)
2) When configuring the printer, confirm whether all parts of the printer are adjusted well and whether the grain meets the specifications, otherwise it should be adjusted as required;
3) Check whether the position of the label header is correct, otherwise it should be adjusted to ensure
a. The outgoing header should be close to the bottle belt and flush with the bottle belt;
b. Use the header to peel the edge of the plate parallel to the bottle bus
d. Adjust the electric eye sensitivity of the label, so that it can detect the sensing points on the label, so as to realize the marking.
4) Check whether the height and width of the conveyor belt guardrail have been adjusted to match the bottle body, and the material should be smoothly passed, otherwise it should be adjusted;
5) Check whether the height and position of the parting wheel have been adjusted to match the bottle body, and the bottle should be uniformly passed, otherwise it should be adjusted;
6) Check whether the position of the push plate is adjusted to match the bottle body, and the distance between the push plate and the bottle belt is slightly less than the diameter of the bottle, so that the label can be smoothly rolled and attached to the bottle body
Second, boot operation
- Turn on the power switch (located on the right of the cabinet).
- Rotate the compressed air switch to the open position and adjust the air pressure to 0.5~0.6Mpa(with printer)
- Tap on the touch screen controller to enter the normal operation page.
- Operation
- Manual operation, check whether all parts have been adjusted properly, whether the operation is smooth, otherwise it should be stopped for adjustment.
- Call and confirm the corresponding product program or enter the “Parameter setting” interface for parameter setting.
Operation
- Manual operation, check whether all parts have been adjusted properly, whether the operation is smooth, otherwise it should be stopped for adjustment.
- Call and confirm the corresponding product program or enter the “Parameter setting” interface for parameter setting. (See Annex 6 for parameter Settings)
- Set the value of each counter as needed.
- Press the Start button to run the machine online and enter the normal production state.
- Press the SCram switch when the device is faulty or in an emergency.
Fourth, Shutdown Procedure
1, press the “Stop” button, the whole system stops, and then turn off the main power switch.
2, in case of emergency, directly press the emergency stop switch, restart the emergency stop switch or power switch, should ensure that the system is in a safe state.
When the machine is not used for a long time, the power cord should be unplugged, the surface of the machine should be clean, and the dust storage should be covered.
Note:
① When the remaining number of labels is equal to or less than the set value, the system will stop and alarm.
② For the printer, see the printer Operation and maintenance manual for the printer adjustment
Powder Filling Machine:
Powder, Liquid, Paste, Granule filling machine Customization:
We have various types of Granule filling machine for sale, and we do customization according to customer’s speed and capacity. We can also design and produce the whole production line including the grinder , Blending machine, drying machine, conveyor, feeder, vibrating Screen, Packing Machine… Please contact us quotation, parameters and price.
LYLK Pneumatic Filling Machine
LYLK Filling and Stoppering machine
LYLK Filling and Capping Machine
LYLK Servo Filling Machine
LYLK Automatic filling and sealing machine
Customize Plastic Bottle Capping Machine According to your Capacity:
We can customize Granule filling machine connect with your production line (the dimension and width of feeder).
Customize Glass Bottle Capping Machine According to your Capacity:
Videos of Filling Machine :
We have many model of Powder, Liquid, granule, paste Filling and Capping Machine , here show some examples:
Production Line Customization Solution:
We can customize whole automatic production line according to customer special request. According to your special material, capacity requirement and motor and electric cabinet certification requirement, we can customize semi-auto or fully automatic production line for our customer. Please contact us for detail proposal and quotation.
Air Below Washing Machine + Sterilize Machine + Filling Machine + Metal Detector + Check Weight + Capping Machine Sealing Machine + Labeling Machine + Label Shrink Film
Drying Machine + Grinding Machine + Sifter Machine + Mixing Machine + Packing Machine:
Factory Information
Factory Information
Business Type: | Manufacturer/Factory | Main Products: | Mill, grinder, granulator, mixer, Crushing Equipment |
Number of Employees: | 100 | Year of Establishment: | 2014.05 |
Production Capacity | 5000 Set/Year | After-sales Service: | Technical Support; on-line teach lessons |
R&D Capacity: | ODM, OEM | Annual Output Value: | US$5 Million – US$10 Million |
No. of R&D Staff: | 5 | No. of Production Lines: | 6 |
Certifications:
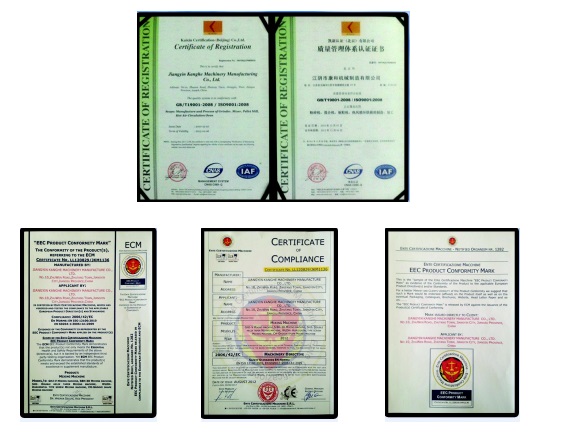
Machine Packing:
Small machine packed with export fumigation-free wooden cases, goes with bulk shipment or in container.
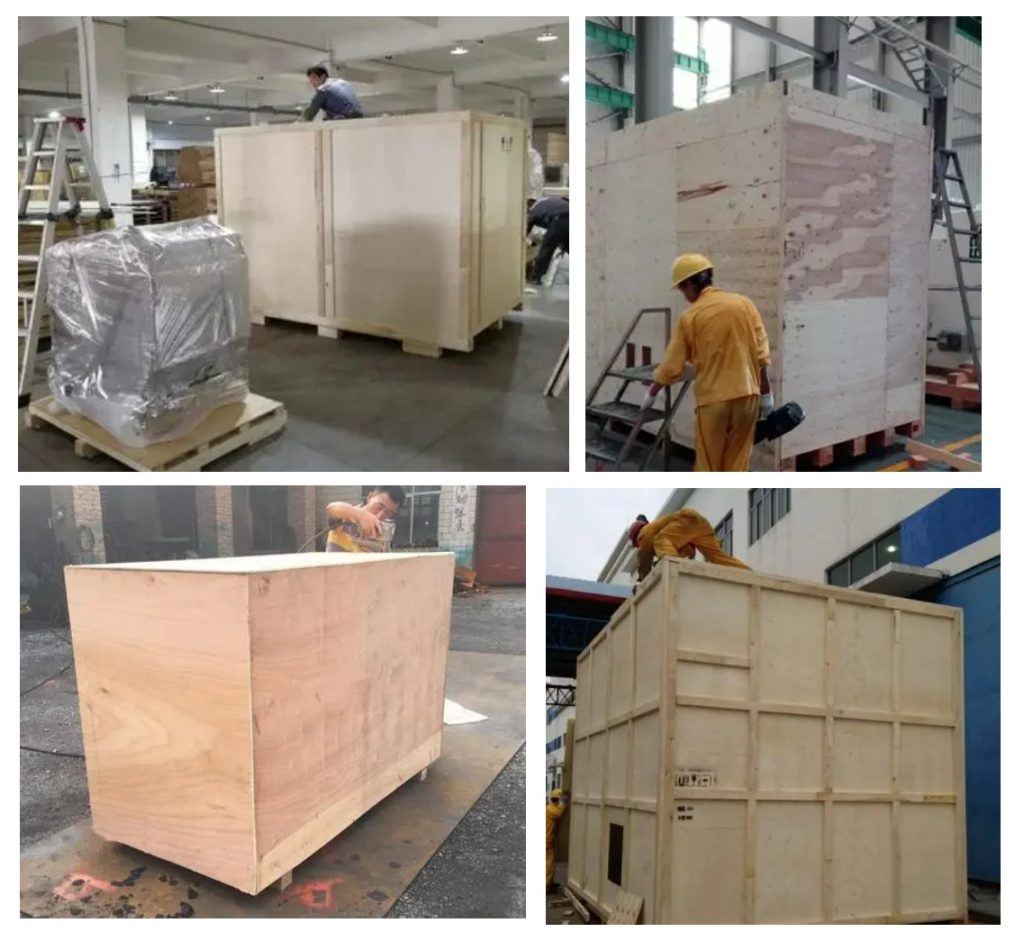
Installation:
- The machine is installed according to the instructions after unpacking, and the compressed air source is connected. If the air source pressure is 0.6MPa, the valve should be installed first in the compressed air main pipeline.
2, open the right door to turn out the oil mist oil label to add clean special oil, or sewing machine oil, note: when the fuel can not be with air pressure, the oil amount of about 8 minutes full is appropriate.
3, the intake air source check whether the sealing surface is leaking, adjust the air pressure to 0.3~0.4MPa to adjust the oil intake, generally spray a drop of oil after several times, regularly check the oil injection.
4, filling volume adjustment: first rotate the filling volume adjustment hand wheel, observe the indicator window scale, so as to achieve the required amount of filling, at the same time adjust the suction, discharge speed to achieve satisfactory filling effect, the dosage standard measure the filling amount, and finally correct the filling amount.
Warranty of Machine:
We provide one year warranty for all our machine, but not including the man-made damage. We can provide free spare parts if damage in one year in normal operation. 24hours stand by to solve urgent problems. 3 days of spare parts provide by express. Please specially notice for the motor connection. it should be connect in right way to prevent the motor burnt, take special notice of running machine safely. Machine need to be clean and maintained frequently.
Maintenance of machine:
Servo filling machine as an important equipment in the automated production line, its maintenance is very important to ensure production efficiency and product quality. The following is an overview of the general servo filling machine maintenance procedures:
Routine maintenance
Cleaning and inspection:
Before and after each shift, clean the external surface of the servo filling machine, especially the working area and transmission components.
Check for debris and foreign objects around the machine and keep the working environment clean and tidy.
Lubrication:
According to the requirements of the equipment manual, regularly fill the lubricating parts of the servo filling machine with appropriate lubricating oil or grease.
Be careful not to over-lubricate or leak to avoid contaminating the product.
Check the transmission components:
Regularly check the tension and wear of the drive belt, chain and gear, and adjust or replace damaged parts in time.
Cleaning and replacing filters:
Regularly clean or replace the servo filling machine air filter, hydraulic filter, etc., to ensure the smooth system and reduce the failure rate.
Scheduled maintenance
Electrical parts inspection:
After powering off the device, check that electrical connections, switches, control panels, and sensors are secure and working properly.
Check cable and wiring wear regularly to avoid short circuit or open circuit.
Pneumatic system maintenance:
Check the working condition of pneumatic components, cylinders and solenoid valves to ensure that the gas path is smooth and there is no leakage.
Servo system calibration:
According to the requirements of the equipment manual, the servo system is calibrated and adjusted regularly to ensure the running accuracy and stability.
Spare parts replacement:
According to the service life of the equipment and the depletion of spare parts, timely replacement of vulnerable parts and key components, such as seals, valves, etc.
Performance test:
Regularly carry out the performance test and function test of the servo filling machine, confirm whether the functions are normal, adjust the parameters and control logic.
Emergency handling
Troubleshooting:
If the device is faulty or abnormal, shut it down immediately and handle it according to the troubleshooting guide in the device manual.
Maintenance records:
Record the specific content, time and operator of each maintenance, and establish maintenance files to facilitate traceability and analysis of equipment operating conditions.
By strictly implementing the above maintenance procedures, the reliability and stability of the servo filling machine can be improved, the service life of the equipment can be extended, and the continuous operation of the production line and the stability of product quality can be ensured.
FAQ
We are factory located in Shanghai China, welcome to visit our team.
1. Normally 30% deposite payment, balance 70% before shipment.
2. We can provide L/C for special country.
1. For some simple machine, we will install before shipment, no need to do complicate install on customer side.
2. For complicate machine, our engineer is available for going customer side, but the visa fee, round flight ticket, hotel and food are undertaken by customer. Besides, engineer compensation 100USD/Day. Engineer can provide installation services, and also available to teach your operator how to use it.
1. Talk with our sales about your product size and applications, capacity you need per minute, For example 50 pcs/minute. we will provide the right mode for you.
2. Place Order and do the first Payment.
3. Produce and send video for your green light.
4. You do the final Payment
5. Arrange shipment
6. Receive goods.