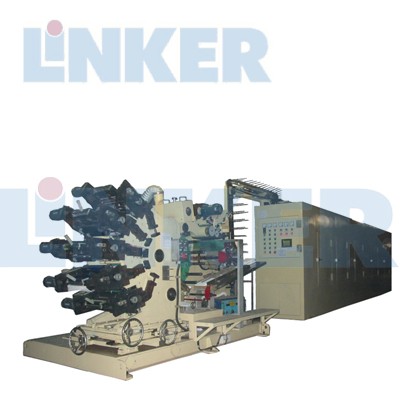
GREAT FEATURE
1-8 color Offset Printing Machine
- Max Speed: 120pcs/minute (Depends on products)
- Color: 1-8 color, customization
- Suitable for : Cosmetic tubes, Silicon Sealants, Aluminum Caps, Paper Cups
- Product Diameter Scope:10~120mm
- Motor Power: Driving Wheel 3.7kw; Driver for printing plate 2.2kw; driver chain 2.2kw; Driver for ink stick 0.06kw
- FOB Price: $115,000.
Applications– Sample of Products
Product dimension: | φ16-φ60mm 20-18-mm depend on products |
Capacity: | 80-100pcs/min |
Motor power for Driving wheel | 3.7KW-1pcs |
Motor for printing plate | 2.2KW–1pcs |
Motor for drive chain | 2.2KW-1pcs |
Motor for driving ink stick | 0.06KW—6pcs |
PrinterMainMotor | 7.5HP(5.5KW) |
Cuttingsystemmainmotor | 3HP(2.2KW) |
Roaster main motor | 3HP(2.2KW) |
Driv emotor | 90W+90W+90W=270W=0.27KW |
UV drying system | 10KW |
Static eliminator system | 1.5KW |
Roaster heating system | 1.2KW*4=4.8KW |
Working air pressure | 0.4-0.8Mpa |
Working voltage | 380V/420V Can customize any Voltage |
External dimensions Printing head : | 3200*1600*1800mm |
Drvingoven:3000kg | 9500*1000*2000mm |
weight Printinghead: | 4000kg |
weight Drying oven: | 3000kg |
No | Name | Remark (maufacturer ) |
1 | Motor | Hanshin |
2 | frequency transformer | Panasonic |
3 | Gear | imported material |
4 | PLC | Mitsubishi |
5 | robot arm system | THK |
6 | Splitter | Japan |
7 | Clutch | Japan |
8 | Feeder System | THK |
9 | Transmission | Schneider |
10 | electronic control | Omoron |
11 | Bearing | Japan |
12 | Cylinder | Japan |
13 | voltage protector | France |
14 | low-voltage apparatus | France |
15 | Big Wheel | CNC |
16 | conveyor | Japan |
17 | Mandrel rods | imported material |
Video
Description:
An 8 color offset printing machine is a highly advanced piece of equipment used for commercial printing. As a manufacturer, producing an 8 color offset printing machine requires significant engineering expertise and experience in the printing industry.
The machine is designed to produce high-quality prints with a wide color gamut and fine resolution. It uses a printing process in which ink is transferred from a metal plate to a rubber blanket, and then onto the soft or hard tube. The use of eight colors in this process allows for a more extensive range of hues and shades, producing highly detailed and vibrant prints.
The machine typically consists of several components, including a feeder unit, printing units, and a delivery unit. Each printing unit is responsible for transferring a specific color to the tube, with the feeder unit providing a steady supply of tube to the printing units. The delivery unit collects the printed sheets and stacks them for further processing or distribution.
As a manufacturer, attention to detail and quality is essential when producing an 8 color offset printing machine. Precision engineering and high-quality materials are critical to ensuring that the machine can produce high-quality prints consistently over time.
Overall, an 8 color offset printing machine is a highly specialized piece of equipment that requires a significant investment in both time and resources to manufacture. However, the end result is a powerful tool that can produce beautiful and vibrant prints that are suitable for a wide range of commercial applications.
Main use of 6 color soft tube printing machine:
It is used for printing 1-6 color(s) and drying tubes.
Features of 6 color soft tube printing machine:
1. Employ precise decollator of 180mm width between centers from TAIWAN to drive the printing table, so as to ensure its stability & long service life under high speed working.
2. To the complex process of shifting tubes from printing table to the chain, we also employ TAIWAN decollator and special made rolling screw rod, to maintain the stability of the work.
3. There is only one data cable connecting the printer and dryer, which brings future convenience to the following situation: if the printer is placed downstair while the dryer is placed on upstairs, the tubes won’t need a lifting machine to convey to upstairs for drying, so as to save manpower.
4. Direct heating of chamber type of dryer reduces heat loss.
5. Gears using in printer is of fine made, which ensure its precision and service life, so as to help precision of chromatography greatly.
6. Dryer is made up of 2 parts, first part is for laminar current and UV treatment, second part is for infrared heating; thanks to a special laminar current, the gloss oil works well, which reduces the count on the smoothness of gloss oil wheel, so as to reduce the grinding to the gloss oil wheel.
7. Back moving design of printing table, when there is no tube on a printing stick, the whole printing table will move backward for 5mm, so as to avoid the contact of ink and printing rod.
8. Matured headless printing helps to reduce the wastage of large area printing, as well as reduce 2 processes–welding & head cutting–for the oval tubes.
Printer Header Pictures
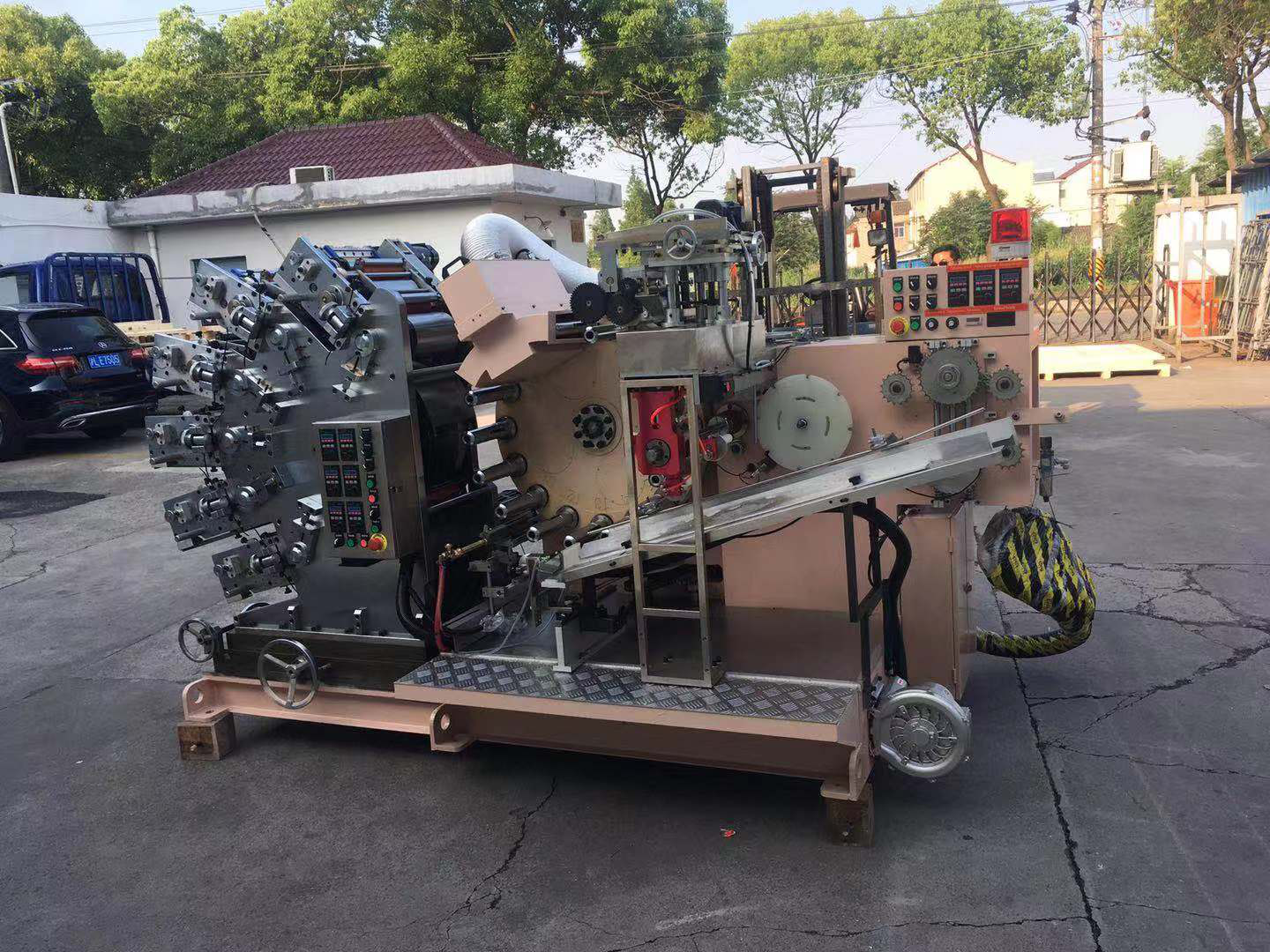

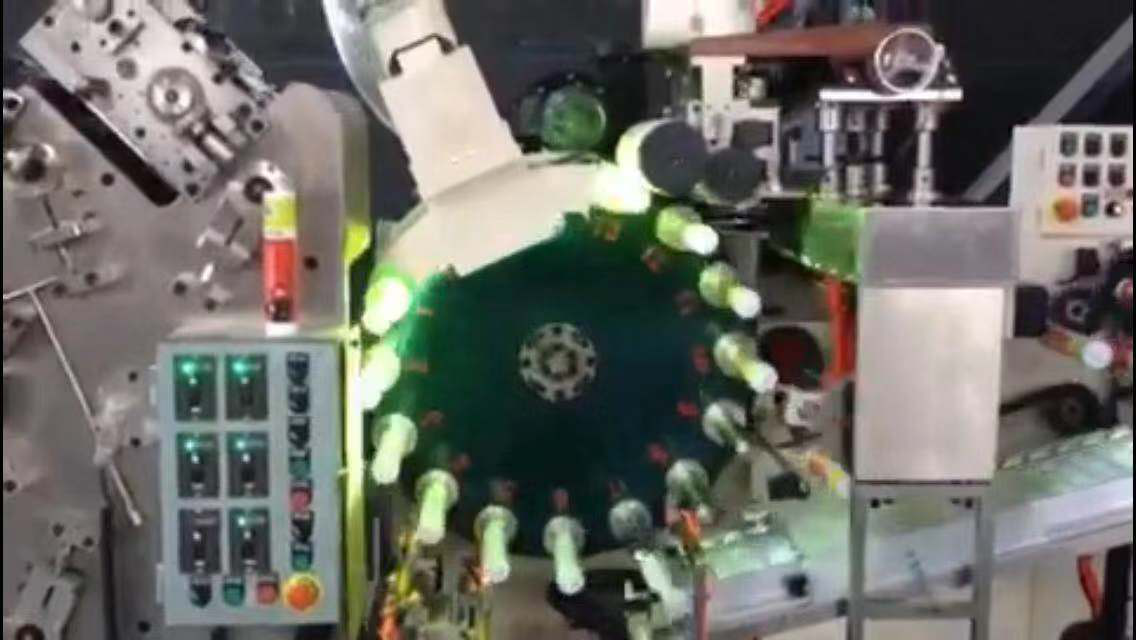
Oven Pictures & Spare Parts
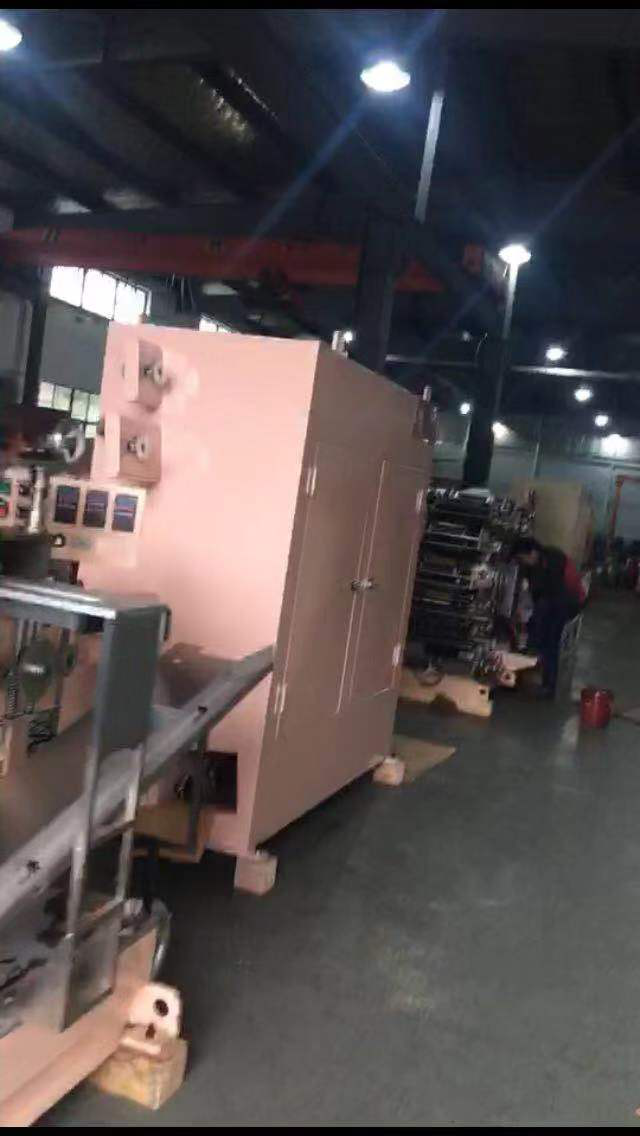
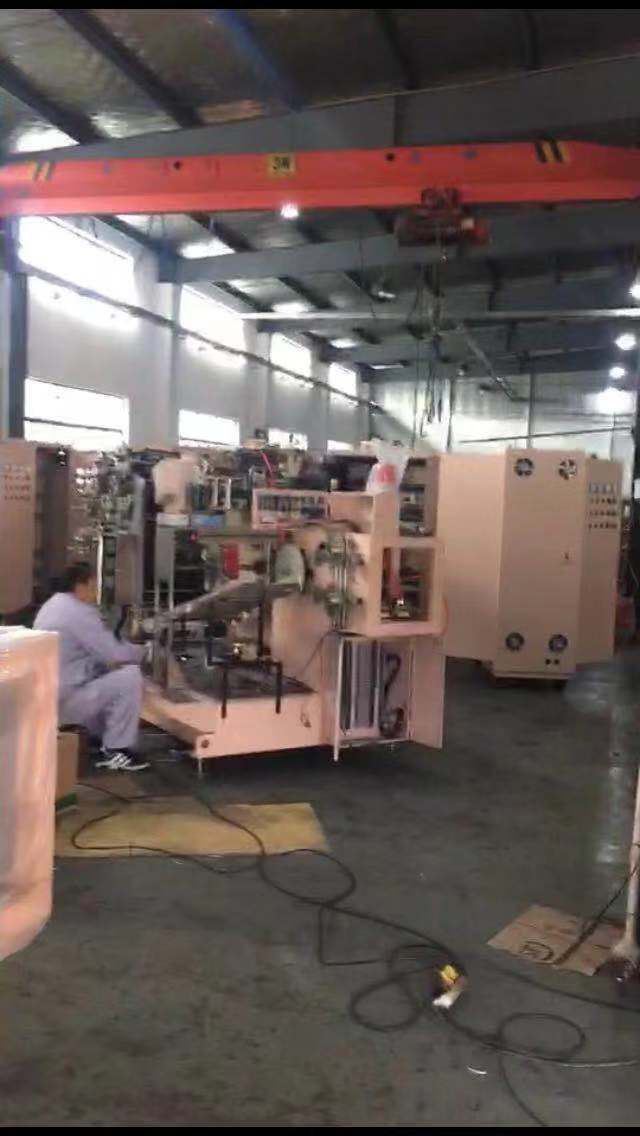
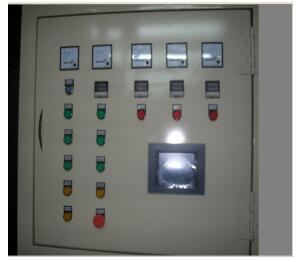
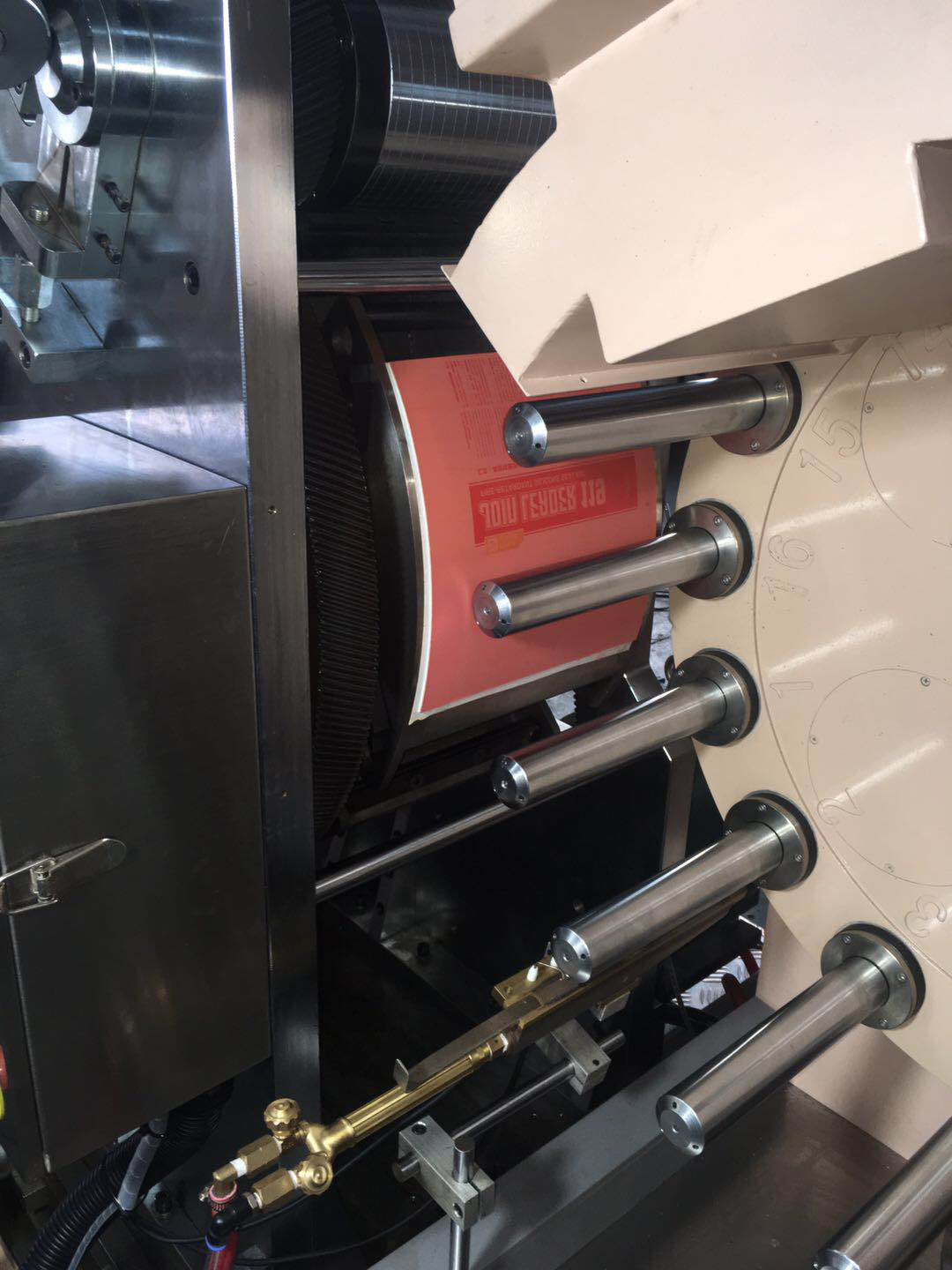
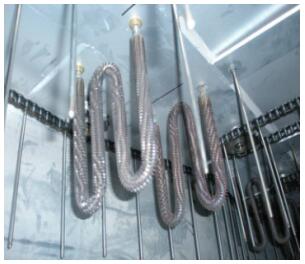
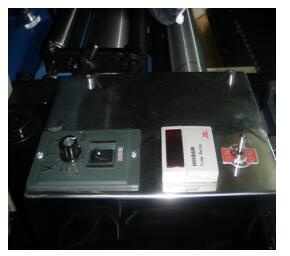