Automatic labeling machine is a device that can paste rolls of paper labels or metal foil labels on PCBS, products or specified packaging. The back of the label comes with adhesive and regularly arranged on the smooth backing paper, and the Feeder or stripping mechanism on the labeling machine can automatically peel it off. The automatic labeling machine locates the PCB or product that flows into the previous link on the production line and confirms its coordinates visually. After the nozzle of the automatic labeling machine takes material at the Feeder, it takes pictures on the bottom camera to confirm the label coordinates. According to the internal algorithm of the machine, the label is aligned with the position coordinates that need to be affixed, and then it is affixed to the product. Has reached a high coating accuracy, automatic labeling machine can complete PCB surface paste, PCB price surface paste, other plane paste, single or multi-sided paste of packaging, cylinder paste, local coverage or full coverage cylinder paste, depression and corner paste and other operations, now the SMT industry has also begun to be widely used to replace manual.
BOPP Labeling Machine
Vial labeling machine
Sticker labeling machine
LYLK Double Sides Jar Labeling Machine
LYLK Round Labeling Machine
LYLK Flat Labeling Machine
LYLK Round bottle labeling machine
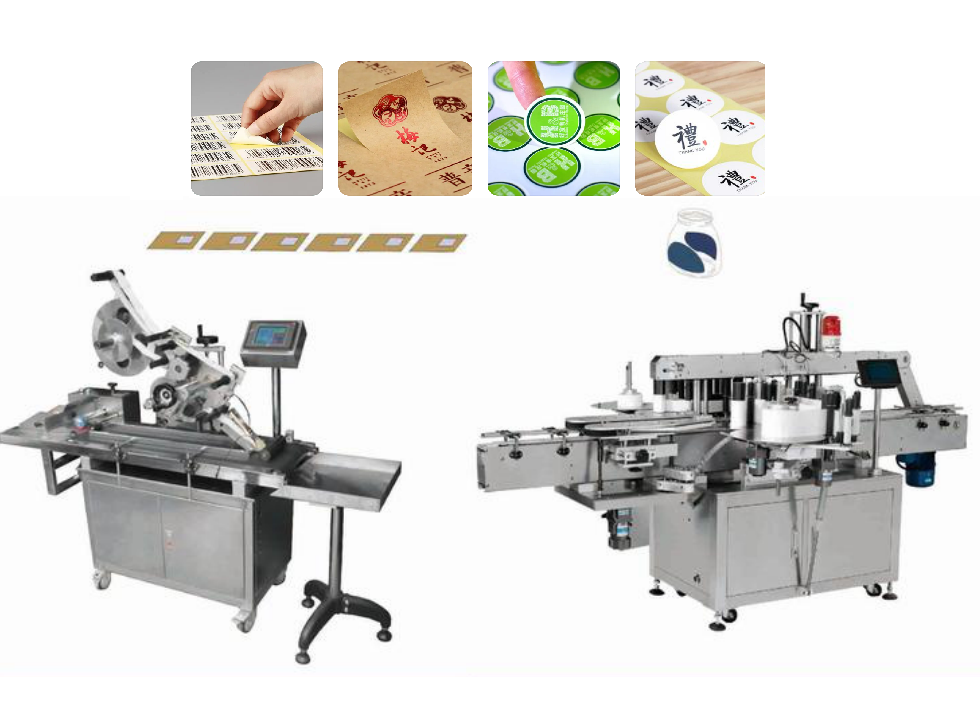
- Width of Label: 20-100mm;
- Length of Label: 20-150mm;
- Speed: 20-40pcs/minute;
- Bottle diameter: 18-20mm;
- Accuracy: within 1mm;
- Price: 500USD.
Suitable for tank diameter 30-300mm, tank height: 40-600mm round or square bottle body, paper tube, etc. for full circle labeling, can also be less than the whole week or the whole body labeling, widely used in food and beverage, pesticide chemical industry, paint and coatings, medicine and health care industry mosquito killer insecticides, air fresheners, self-painting, expanding glue, butane gas, leather polishing agent and other items packaging.
Automatic labeling mechanism:
Japanese industrial computer automatic control electrical system (English and Chinese interface), RTM servo motor, pneumatic parts Taiwan pneumatic parts, American color test.
Working steps: All the processes of tank automatic import, label cutting, gluing, positioning, attaching, pressing and label heat shrink tightening at the upper and lower mouth of the tank are automatically completed, and it has a 15-phase alarm system.
Labeling quality: complete cutting pattern, no deformation; Terminal mesh gluing, compared with foreign full-spray gluing equipment, saving thermal sol 50%; Correction ±0.05 (mm); Upper and lower labels heat shrink tight without wrinkling; The overall labeling surface is smooth, no misalignment, no leakage, no opening.
Performance indicators: Labeling speed: 40-80 (bottles/min); Dimensions: 210013001600mm; Power: 3.6 kW; Total weight: 900kg
Construction
Conveyor belt: used to transport products to be labeled and labeled products, driven by 60W3 PVC, belt conveyor belt;
Labeling host: used to drive the entire volume of labels and peel off a single label to supply products. It is composed of stepper motor, polyurethane marking wheel, marking plate, guide shaft, brake mechanism, marking mechanism, stripping plate, synchronous receiving mechanism, lifting mechanism and adjusting mechanism.
Labeling position adjustment: used to control the labeling of products of different heights and the labeling of the left and right positions of products. The hand wheel drives the labeling motherboard to move up and down to control the position of the labeling board, so as to adjust the labeling degree and the position before and after.
Power control: Used to switch the total power supply and control and indicate the power supply.
Man-machine interface: used to control the automatic operation program, in the man-machine interface can separately control part of the action and in the man-machine interface can set, store, read a variety of label operation parameters
Brush marking device: used for product labeling when the brush brushes the label flat on the surface of the product.
Main electrical box: Used to install the main electrical control components of the equipment, such as stepper motor driver, voltage regulator power supply, transmission motor inverter, program controller (PLC)
How to adjustment:
1, because the location of the measurement eye is related to the timing of the label, so to adjust its position, the position required for different sizes of bottles is different, if the location of the measurement eye is too late, there will be premature labeling, resulting in labeling too early, and even will not be labeled. If the electric eye of the measurement object is too far ahead, it will be marked too late, resulting in skewed labeling or labeling the queen. (Before and after the operator is facing the human-machine interface, the direction of the bottle in the conveyor belt forward is the front) 2, and the marking eye is related to the marking position and the length of the marking in advance, so it is also necessary to adjust its position, the position required for different labels may also be different, if the position of the marking eye is too high, the pre-marking is not enough, resulting in the labeling is not allowed. Or label it back. If the position of the marker eye is too low, there will be too many pre-marked, resulting in wrinkled labeling, or labeling forward.
Application
The labeling machine is mainly used for automatic labeling of the upper plane (top surface) of various shapes of products suitable for vertical placement in medicine, daily chemical industry, food, etc. Adopt high precision and high speed labeling device, adapt to a variety of different size range of product labeling. Save a lot of manpower, improve labeling accuracy and consistency; Adopt imported high-precision intelligent eye and high-reliability microcomputer chip program controller (PLC) stepper motor labeling, and adopt human-machine interface humanized graphic display control, operation and setting intuitive and convenient, and has 50 groups of parameter storage and counting stop function.
Guanhao labeling machine interface basic operation
◇ Main material matching on the main interface of the touch screen of the labeling machine
◇ Auxiliary material matching on the main interface of the touch screen of the labeling machine
◇ Press the stop button on the main interface of the touch screen of the labeling machine to stop production
◇ Press the start button on the touch screen main interface of the labeling machine to start production
◇ Set the label length according to the label size on the touch screen main interface of the labeling machine
◇ Set the length of the bottom material according to the size of the bottom material on the main interface of the touch screen of the labeling machine
◇ Set the production quantity according to the production situation on the main interface of the touch screen of the labeling machine
◇ Turn on the counting function on the main interface of the touch screen of the labeling machine for production counting
◇ Set the main speed and bonding speed on the touch screen main interface of the labeling machine according to the production situation
◇ Turn on the automatic function on the main interface of the touch screen of the labeling machine to enter the automatic control mode
◇ Press the emergency stop button on the main interface of the touch screen of the labeling machine to stop production, but it can be restarted only after re-matching
◇ Set the number of lost labels on the main interface of the touch screen of the labeling machine, generally set to zero, which is used to control the processing of the lost color label
◇ In the main interface of the touch screen of the labeling machine according to the production process, if the label deviation, you can enter the phase size on the main interface of the touch screen to adjust the longitudinal deviation, and adjust the horizontal deviation through the horizontal handle.
Manual interface operation of labeling machine
◇ When the labeling machine is abnormal and needs manual operation, press the click button on the touch screen main interface to enter the manual interface
◇ Set the moving length on the touch screen main interface
◇ On the main interface of the touch screen, CX can control the movement of the auxiliary shaft, CY can control the movement of the label head, and CZ can control the movement of the main material shaft
Label machine tension interface operation
◇ When the labeling machine needs to operate the tension, press the tension button on the main interface of the touch screen to enter the tension interface
◇ On the touch screen tension interface, control the start and stop of the feed shaft, tension size and direction; Control the start, stop, tension and direction of the receiving shaft of the main material shaft; Control the start and stop, tension and direction of the auxiliary material receiving shaft.
Self-adhesive labeling machine warping phenomenon solution
To achieve perfect visual effect in labeling. One of them is to avoid warping in labeling. Label the pipe before it is not filled, and then fill and seal the end after it is pasted, and the heating in the process of sealing the label is particularly severe, and the closer the label is to the bottom, the greater the possibility of warping the mark. In practical applications, almost every manufacturer has similar problems, and there are various solutions:
(1) Increase the viscosity of the label and try to make the label stick firmly. To achieve this effect, the following aspects should be considered:
① Improve the surface quality of the attached hose. Most products have light oil on the surface, which will increase the difficulty of labeling, the seepage of the contents, the microholes in the tube wall, and so on, will cause the warping of the label. How to avoid such problems should be a more important issue for everyone to consider.
② Control the labeling pressure of the label during the labeling process.
③ Control the temperature during the labeling process. Increasing the labeling temperature will improve the labeling effect, because with the increase in temperature, the activity of the material inside the object will increase, and the label will be easier to integrate with the tube body.
(2) Try to use soft label materials, and good label ductility will also greatly improve the warping mark.
(3) Change the shape of the label.
Shape the bottom end of the label into an arc to avoid the deformation area of the tail sealing. Of course, the arc can not be opened too deep, otherwise it is easy to cause wrinkles due to the problem of the label itself, and increase unnecessary trouble. For the special-shaped sealing end, the shape of the label is required to be changed accordingly, which can not only avoid the warp mark but also increase the beauty.
(4) Eliminate the influence of static electricity.
The labeling process is easy to produce static electricity, which will affect the labeling effect, appropriately improve the humidity of the labeling site, there will be a certain improvement, the use of ion fan is also an effective solution. The labeling machine is equipped with automatic humidity control, and the cleanliness inside the equipment can be controlled separately to keep the labeling away from dust and improve the labeling quality of the product. In this way, there is no longer a warping phenomenon in the labeling process, and the visual effect is achieved.
Parameter
Suitable for tank diameter 30-300mm, tank height: 40-600mm round or square bottle body, paper tube, etc. for full circle labeling, can also be less than the whole week or the whole body labeling, widely used in food and beverage, pesticide chemical industry, paint and coatings, medicine and health care industry mosquito killer insecticides, air fresheners, self-painting, expanding glue, butane gas, leather polishing agent and other items packaging.
Automatic labeling mechanism:
Japanese industrial computer automatic control electrical system (English and Chinese interface), RTM servo motor, pneumatic parts Taiwan pneumatic parts, American color test.
Working steps: All the processes of tank automatic import, label cutting, gluing, positioning, attaching, pressing and label heat shrink tightening at the upper and lower mouth of the tank are automatically completed, and it has a 15-phase alarm system.
Labeling quality: complete cutting pattern, no deformation; Terminal mesh gluing, compared with foreign full-spray gluing equipment, saving thermal sol 50%; Correction ±0.05 (mm); Upper and lower labels heat shrink tight without wrinkling; The overall labeling surface is smooth, no misalignment, no leakage, no opening.
Performance indicators: Labeling speed: 40-80 (bottles/min); Dimensions: 210013001600mm; Power: 3.6 kW; Total weight: 900kg
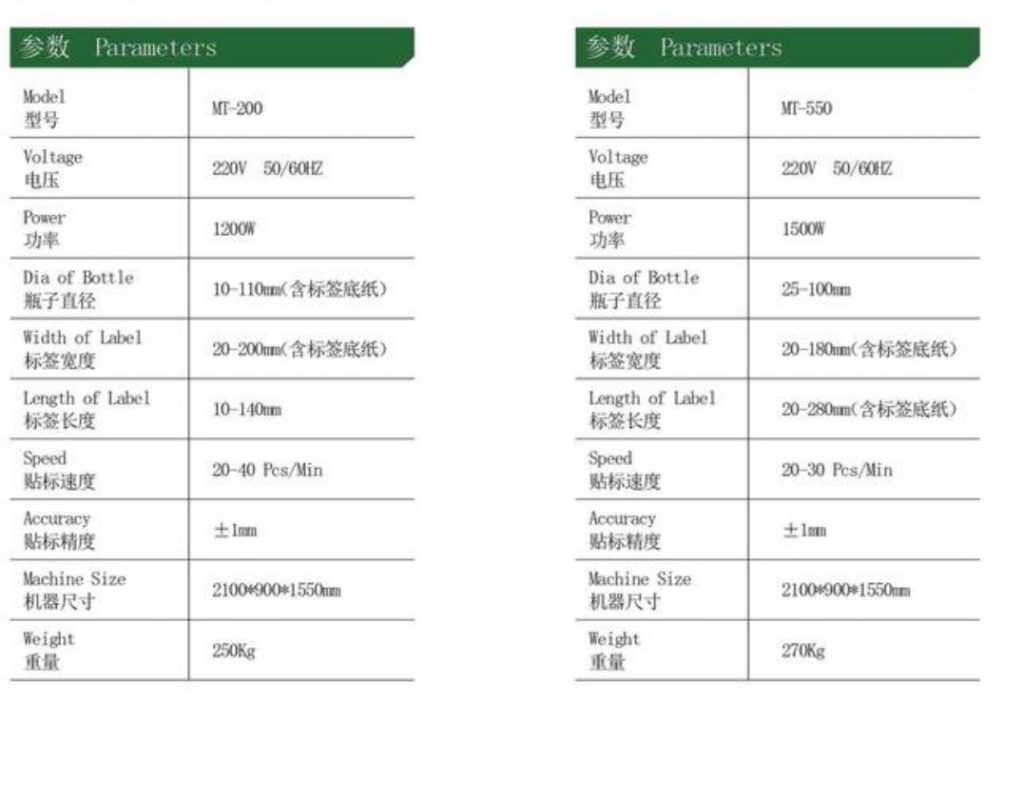
Automatic labeling machine for a long time will inevitably appear some failures, today on the automatic labeling machine often appear problems are listed, hope to bring you help:
- Adjustment of brush press device.
The center of the brush is aligned with the label and symmetrical on both sides. The marker brush is perpendicular to the surface of the container. The overlap gap between the brush and the container is 10mm to 15mm for a single brush and 5mm to 10mm for a combined brush. The distance between the cleaning brush and the sponge should be 1mm to 2mm. Pressure head adjustment. The pressing head should be 20mm lower without the bottle than with the bottle. - Adjust the label box.
The center line of the label box, the center axis of the label station and the label paper are tangent, the center axis of the label board is in a line at three points, adjust the tangent of the label board and the label paper (0 distance), and then move the label box closer to 1mm ~ 2mm. The gap between the label paper and the two sides of the bar should be between 0.8mm-1mm, the gap is too large to cause the label paper to shift in the label box, and the skew mark appears, and the gap is too small to cause the push mark. Adjustment of the position of the hook of the box: the hook of the upper and lower, left and right are on the same vertical plane and are evenly labored on the marking paper, so that the mark can be grasped smoothly. The label provides roller adjustment: When there is no label, the label pressure plate can be pressed to the most front of the label box and the label near the hook finger cannot be crushed. - Adjustment of star wheel in bottle, star wheel out bottle and screw rod in bottle.
When adjusting the star wheel and screw rod in and out of the bottle, the bottle pressing head of the marking machine shall prevail. First adjust the inlet star wheel, when the bottle press head is just over the bottle, adjust the inlet star wheel so that the bottle is in the middle of the star wheel groove. Adjustment of the screw into the bottle: when the bottle is in the middle of the groove of the star wheel into the bottle, adjust the screw so that the screw into the bottle side is tight to the bottle but does not displace. Exit star wheel adjustment: When the press head is just raised, adjust the star wheel so that the bottle is in the middle of the groove of the star wheel. - Standard station adjustment.
Adjustment of scraping plate and roller: there can be no gap between the scraping plate and the roller in the entire length. If there is a gap, the scraping plate can be adjusted by adjusting the eccentric bolt. Adjustment of the roller and the plate: the plate and the roller only contact each other without any pressure. The gap is too large, too much glue on the plate, resulting in glue. If the gap is too small and the contact is too tight, the glue will be squeezed away, and there is no glue on one side of the label board. Practice has proved that the gap between the label plate and the roller is between 0.1mm and 0.2mm. This can be achieved by adjusting the bearing seat on the lower part of the roller, and adjusting the bearing on the upper part of the roller if necessary.
Product Information
Powder Filling Machine:
Powder, Liquid, Paste, Granule filling machine Customization:
We have various types of Granule filling machine for sale, and we do customization according to customer’s speed and capacity. We can also design and produce the whole production line including the grinder , Blending machine, drying machine, conveyor, feeder, vibrating Screen, Packing Machine… Please contact us quotation, parameters and price.
LYLK Pneumatic Filling Machine
LYLK Filling and Stoppering machine
LYLK Filling and Capping Machine
LYLK Servo Filling Machine
LYLK Automatic filling and sealing machine
Customize Plastic Bottle Capping Machine According to your Capacity:
We can customize Granule filling machine connect with your production line (the dimension and width of feeder).
Customize Glass Bottle Capping Machine According to your Capacity:
Videos of Filling Machine :
We have many model of Powder, Liquid, granule, paste Filling and Capping Machine , here show some examples:
Production Line Customization Solution:
We can customize whole automatic production line according to customer special request. According to your special material, capacity requirement and motor and electric cabinet certification requirement, we can customize semi-auto or fully automatic production line for our customer. Please contact us for detail proposal and quotation.
Air Below Washing Machine + Sterilize Machine + Filling Machine + Metal Detector + Check Weight + Capping Machine Sealing Machine + Labeling Machine + Label Shrink Film
Drying Machine + Grinding Machine + Sifter Machine + Mixing Machine + Packing Machine:
Factory Information
Factory Information
Business Type: | Manufacturer/Factory | Main Products: | Mill, grinder, granulator, mixer, Crushing Equipment |
Number of Employees: | 100 | Year of Establishment: | 2014.05 |
Production Capacity | 5000 Set/Year | After-sales Service: | Technical Support; on-line teach lessons |
R&D Capacity: | ODM, OEM | Annual Output Value: | US$5 Million – US$10 Million |
No. of R&D Staff: | 5 | No. of Production Lines: | 6 |
Certifications:
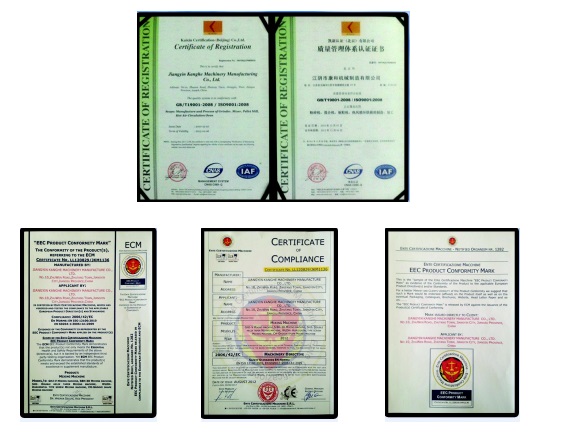
Machine Packing:
Small machine packed with export fumigation-free wooden cases, goes with bulk shipment or in container.
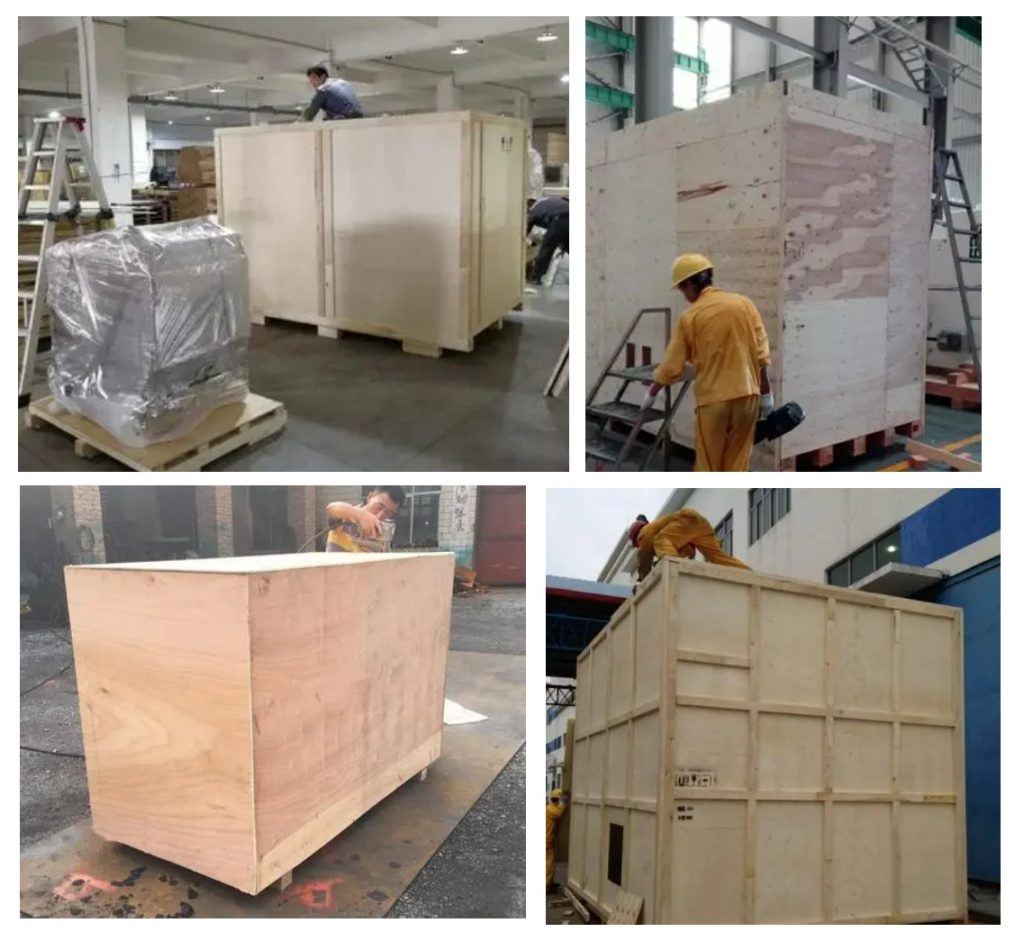
Installation:
- The machine is installed according to the instructions after unpacking, and the compressed air source is connected. If the air source pressure is 0.6MPa, the valve should be installed first in the compressed air main pipeline.
2, open the right door to turn out the oil mist oil label to add clean special oil, or sewing machine oil, note: when the fuel can not be with air pressure, the oil amount of about 8 minutes full is appropriate.
3, the intake air source check whether the sealing surface is leaking, adjust the air pressure to 0.3~0.4MPa to adjust the oil intake, generally spray a drop of oil after several times, regularly check the oil injection.
4, filling volume adjustment: first rotate the filling volume adjustment hand wheel, observe the indicator window scale, so as to achieve the required amount of filling, at the same time adjust the suction, discharge speed to achieve satisfactory filling effect, the dosage standard measure the filling amount, and finally correct the filling amount.
Warranty of Machine:
We provide one year warranty for all our machine, but not including the man-made damage. We can provide free spare parts if damage in one year in normal operation. 24hours stand by to solve urgent problems. 3 days of spare parts provide by express. Please specially notice for the motor connection. it should be connect in right way to prevent the motor burnt, take special notice of running machine safely. Machine need to be clean and maintained frequently.
Maintenance of machine:
Servo filling machine as an important equipment in the automated production line, its maintenance is very important to ensure production efficiency and product quality. The following is an overview of the general servo filling machine maintenance procedures:
Routine maintenance
Cleaning and inspection:
Before and after each shift, clean the external surface of the servo filling machine, especially the working area and transmission components.
Check for debris and foreign objects around the machine and keep the working environment clean and tidy.
Lubrication:
According to the requirements of the equipment manual, regularly fill the lubricating parts of the servo filling machine with appropriate lubricating oil or grease.
Be careful not to over-lubricate or leak to avoid contaminating the product.
Check the transmission components:
Regularly check the tension and wear of the drive belt, chain and gear, and adjust or replace damaged parts in time.
Cleaning and replacing filters:
Regularly clean or replace the servo filling machine air filter, hydraulic filter, etc., to ensure the smooth system and reduce the failure rate.
Scheduled maintenance
Electrical parts inspection:
After powering off the device, check that electrical connections, switches, control panels, and sensors are secure and working properly.
Check cable and wiring wear regularly to avoid short circuit or open circuit.
Pneumatic system maintenance:
Check the working condition of pneumatic components, cylinders and solenoid valves to ensure that the gas path is smooth and there is no leakage.
Servo system calibration:
According to the requirements of the equipment manual, the servo system is calibrated and adjusted regularly to ensure the running accuracy and stability.
Spare parts replacement:
According to the service life of the equipment and the depletion of spare parts, timely replacement of vulnerable parts and key components, such as seals, valves, etc.
Performance test:
Regularly carry out the performance test and function test of the servo filling machine, confirm whether the functions are normal, adjust the parameters and control logic.
Emergency handling
Troubleshooting:
If the device is faulty or abnormal, shut it down immediately and handle it according to the troubleshooting guide in the device manual.
Maintenance records:
Record the specific content, time and operator of each maintenance, and establish maintenance files to facilitate traceability and analysis of equipment operating conditions.
By strictly implementing the above maintenance procedures, the reliability and stability of the servo filling machine can be improved, the service life of the equipment can be extended, and the continuous operation of the production line and the stability of product quality can be ensured.
FAQ
We are factory located in Shanghai China, welcome to visit our team.
1. Normally 30% deposite payment, balance 70% before shipment.
2. We can provide L/C for special country.
1. For some simple machine, we will install before shipment, no need to do complicate install on customer side.
2. For complicate machine, our engineer is available for going customer side, but the visa fee, round flight ticket, hotel and food are undertaken by customer. Besides, engineer compensation 100USD/Day. Engineer can provide installation services, and also available to teach your operator how to use it.
1. Talk with our sales about your product size and applications, capacity you need per minute, For example 50 pcs/minute. we will provide the right mode for you.
2. Place Order and do the first Payment.
3. Produce and send video for your green light.
4. You do the final Payment
5. Arrange shipment
6. Receive goods.